Top 8 Benefits of Progressive Die Stamping
Progressive die stamping is highly effective and efficient for crafting high-quality products. Its many benefits have become an increasingly popular choice among manufacturers looking to create durable and consistent products.
This article will discuss the top 8 benefits of progressive die stamping, including its ability to produce precise and consistent results, reduce waste, streamline production processes, improve manufacturability, and reduce overall costs.
- Consistency
- Efficiency
- Durability
- Customization
- Variety
- Cost-effectiveness
- Reduced production time
- Reduced material waste
Table of Contents
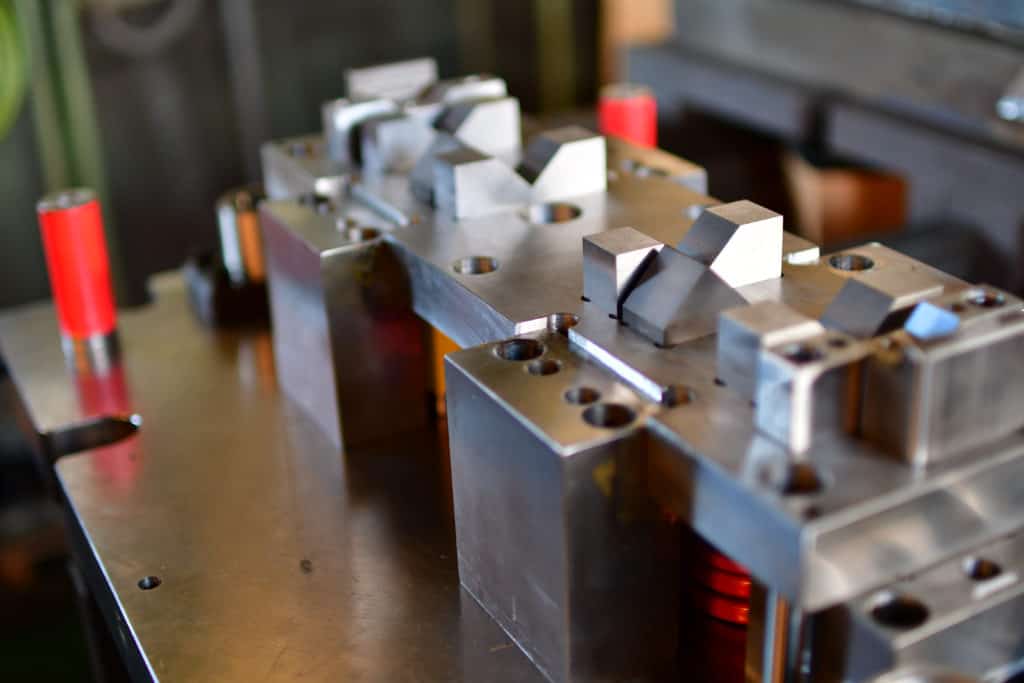
- Consistency: Progressive die stamping produces consistent, high-quality products due to its precise nature. This means that each item created with this method will have the exact dimensions and level of quality, regardless of how often it is produced or which machines are used.
- Efficiency: Progressive die stamping is a fast and efficient process, allowing manufacturers to produce large quantities of products in a shorter amount of time. This helps businesses keep up with demand and reduces costs by increasing production speed without sacrificing quality.
- Durability: With high precision, progressive die stamping can create durable products that withstand heavy use and wear. This makes it ideal for various products, from consumer goods to industrial components.
- Customization: Progressive die stamping allows manufacturers to easily customize their products through material selection or design tweaks. This gives businesses greater flexibility in creating the exact effects that their customers need and want.
- Variety: Because progressive die stamping can be used to create a wide range of different products, it is an ideal choice for businesses that want the flexibility to offer their customers various options. Whether you need custom-made parts for your machine or unique packaging for your consumer goods, progressive die stamping can help you achieve your goals.
- Cost-effectiveness: One of the enormous benefits of progressive die stamping is its ability to reduce overall costs. With its high efficiency and accuracy, this method allows manufacturers to produce products at a lower price while maintaining high standards of quality.
- Reduced production times: Progressive die stamping also allows manufacturers to reduce production times, which can help them save money and stay competitive in a fast-paced market.
- Reduced material waste: In addition, progressive die stamping helps reduce material waste by eliminating many inefficiencies that often occur during manufacturing processes.
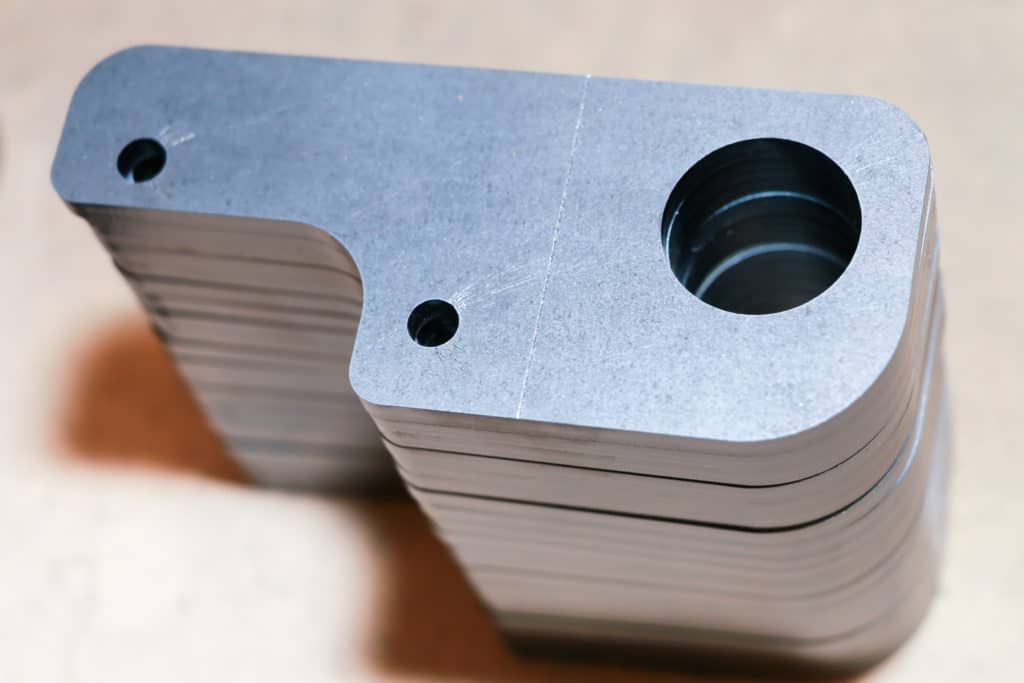
How to take advantage of Progressive Die Stamping?
Progressive Die Stamping is a manufacturing process that feeds the material through different working parts and dies stations.
This can be considered one of the most efficient production methods, and when used correctly, it can provide excellent results for your business. Here are some tips that will help you take advantage of this method:
- Consider your materials and the tooling requirements carefully – This is one of the most critical steps in Progressive Die Stamping. You must consider your material and the types of dies required, as this will help you choose a suitable process for your needs.
- Invest in high-quality equipment – Another critical aspect of Progressive Die Stamping is the quality of the equipment that you use. Make sure to invest in high-quality tools and dies, as this will help ensure your process goes smoothly without any issues.
- Select a reliable partner – Finally, working with a reputable partner who can provide excellent technical support, maintenance services, and more is vital. And will help to ensure that you can take full advantage of Progressive Die Stamping and achieve your production goals.
If you want to take advantage of Progressive Die Stamping, you can achieve excellent results in your production process and create high-quality products by following these tips.
Whether you are looking to launch a new product or improve an existing one, Progressive Die Stamping can help you accomplish your goals.
Ready to get your parts?
How can progressive die-stamping operations be optimized?
One of the keys to optimizing progressive die stamping operations is focusing on performance and repeatability. This involves carefully monitoring and adjusting your process parameters to achieve optimal alignment between the workpiece, dies, and press that will produce consistent results.
In addition, you should also consider ways to improve part quality by minimizing variation in the stamping process itself. Some critical best practices to keep in mind when optimizing your progressive dies include:
- Pay close attention to the part design and material specifications, as these will significantly impact the success of your die stamping operation. For example, choosing a material that is too hard or too soft can lead to issues such as spring-back and die wear, while features that are too thin or brittle may not withstand the stamping process.
- Invest in high-quality dies explicitly designed for your application. This will help ensure that the dies can stand up to the demands of a progressive die stamping operation and produce consistently good results over time.
- Maintain your dies and press equipment regularly, and replace worn parts to keep your process running smoothly. This will help minimize downtime and ensure that quality results are consistently achieved with each stamping run.
- Pay close attention to the set-up of your die stamping equipment to achieve optimal alignment and proper functioning. This may require regular adjustments, such as re-positioning the dies to gain the appropriate clearance between them.
- Invest in process monitoring tools that can help you monitor key stamping parameters, including die wear, tonnage, and cycle time. Such tools can be a valuable aid in optimizing your stamping operation for optimal performance and repeatability.
By following these best practices, you can ensure that your progress dies stamping operation runs at peak performance and produces consistent, high-quality parts each time.
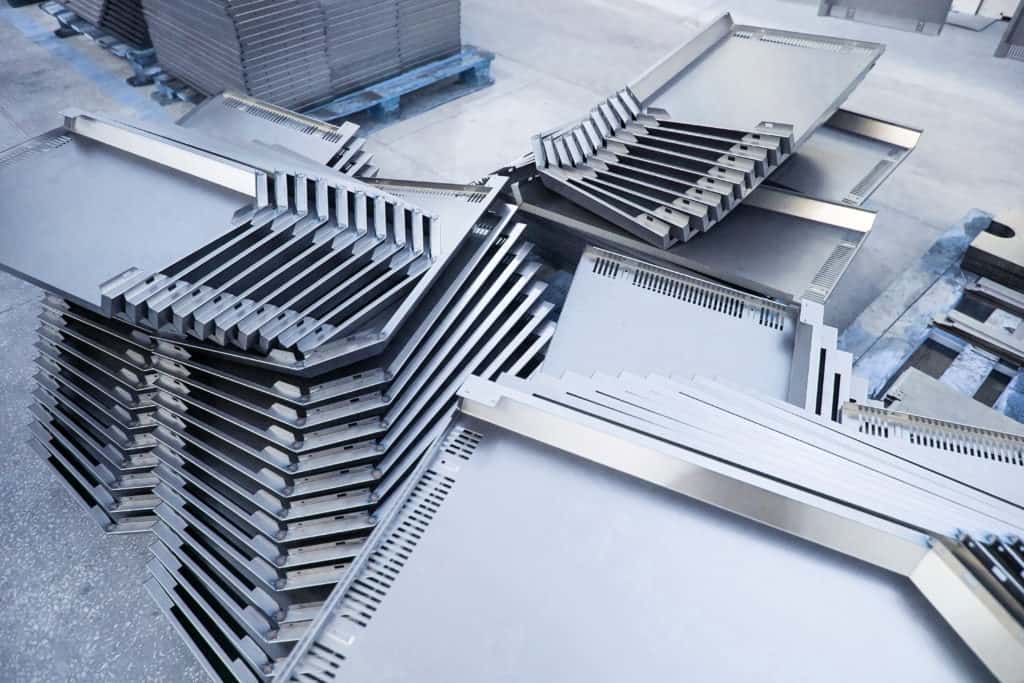
How to ensure my stamping dies or mold lasts as long as possible?
One of the most important things you can do to extend the life of your stamping dies or molds is to ensure that you use high-quality materials and lubricants.
For example, it’s a good idea to choose metals like stainless steel or tool steel for your dies, as these materials are more durable and less likely to wear or break down over time.
Additionally, you should use high-quality lubricants when operating your dies and molds. This can help reduce friction and heat buildup, damaging your dies and shortening their lifespan.
Another critical factor in extending the life of your stamping dies or molds is ensuring that they are adequately cleaned and maintained.
This means regularly removing any debris and residue that may have built up inside your dies or molds and ensuring that you are using the correct cleaning solutions.
Additionally, it’s essential to pay close attention to the wear on your dies or molds as well, as this can help you identify potential problems before they become more severe and lead to damage.
If you’re looking for additional tips on extending the life of your stamping dies or molds, it’s a good idea to speak with an experienced tooling expert or manufacturer.
They can help you understand the unique needs and challenges of your die or mold manufacturing process and offer recommendations on how best to care for your dies or molds based on their experience.
Using these tips, you can ensure that your stamping dies or molds last as long as possible and avoid the expense and hassle of having to replace them early.
Need your parts within 2 days? We've got 2 days lead time
Progression dies stamping's common challenges
Progress die stamping is one of the most challenging processes in metalworking, requiring a high degree of precision and attention to detail.
Several common challenges can arise during this process, such as uneven material flow, warped or deformed dies, and inaccurate positioning. Fortunately, several ways exist to overcome these challenges and achieve success in progress die stamping.
One of the most important things to consider when working with dies in progress die stamping is ensuring that your material flow is smooth and even.
This can be accomplished by setting up your machine correctly, adjusting the pressure of your press as needed, and monitoring the position of your dies throughout the process.
Another common challenge in progress die stamping is dealing with warped or deformed dies. This can often be caused by moisture exposure, improper storage, and uneven heating.
If you encounter warped or twisted dies in your process, it is essential to address this issue immediately to avoid further damage and maintain quality results.
To complete progress die stamping, it is also important to carefully position your dies. This can be achieved by using precision measuring tools, making incremental adjustments to the position of the dies as needed, and keeping careful records of all changes made during the process.
With proper preparation, attention to detail, and careful positioning, you can complete progress die stamping and achieve the high-quality results you need. Whether working with new dies or replacing old ones, it is crucial to approach the process with patience, flexibility, and focus to achieve success.
Frequently asked questions
First, you will need to determine whether your required design can be manufactured with a standard stamping die or whether you will need a custom-made one. Generally, most standard stamping dies can accommodate basic design requirements with minor modifications. However, a customized die may be required if a stamping die is needed for a more complex design or a specific purpose.
One of the critical factors to consider when designing your custom-made stamping die is the type and thickness of the material that you will be working with. Different materials, such as metals and plastics, require different types of dies to produce high-quality results. For example, a standard stamping die may work well for stamping thin metal sheets, but more is needed to make the desired results in thicker materials. Overall, you can customize the stamping die for your product, but we recommend speaking to our engineers and designers for expert advice.
Regarding stamping parts, we understand that there may be some challenges that you will need our support with to get the most out of your pieces. For example, we can help you with forming and shaping, heat treatment, finishing, assembly, designing, and engineering. Additionally, our team can provide guidance and recommendations for optimizing your parts for specific processes and offer suggestions on material selection. No matter what challenges you may face when working with stamping parts, we are here to help you get the most out of your investment in these components.
To ensure that your dies are correctly aligned and registered when stamping parts, it is essential to consider several different factors. Some key considerations include the shape and size of your dies and the type and thickness of the material you stamp. Additionally, consider using a calibration plate or alignment block to ensure that the dies are appropriately aligned. Ultimately, using these methods and considering these factors can help you ensure high-quality results when stamping parts.