Table of Contents
Understanding Feed Rate
Definition of Feed Rate
- Feed in machining Feed rate, also known as feed speed, refers to the linear motion of the cutting tool or workpiece relative to each other during a machining operation. The machining process’s efficiency and quality depend significantly on measuring its speed, usually expressed in inches per minute (IPM) or millimeters per minute (mm/min).
- Feed in metal machining In metal machining, the feed rate determines the rate at which the cutting tool removes material from the workpiece. Increasing the feed rate will lead to a quicker removal of material, but reducing the feed rate will result in better accuracy during the cutting process.
- Feed-in cutting machine In a cutting machine, the feed rate controls the movement of the cutting tool relative to the workpiece. It affects the chip thickness, which in turn impacts the quality of the cut and the overall machining process.
- Feed in manufacturing In the manufacturing industry, the feed rate is a vital parameter that affects the performance and efficiency of various machining operations, including milling, turning, and drilling. By optimizing the feed rate, manufacturers can improve the quality of the machined parts while reducing production time and tool wear.
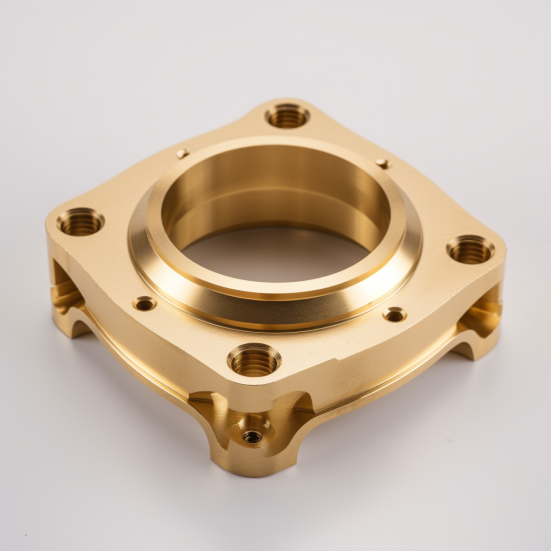
Importance of Feed Rate
The feed rate is essential for several reasons. It directly affects the surface finish, tool life, and machining time. A suitable feed rate ensures efficient material removal, minimizing tool wear and improving productivity. On the other hand, an incorrect feed rate can lead to poor surface finish, increased tool wear, and reduced efficiency.
Factors Affecting Feed Rate
Cutting tool material The material of the cutting tool impacts the feed rate. Softer cutting tool materials, such as high-speed steel (HSS), typically require lower feed rates than harder materials like carbide or ceramic, which can withstand higher feed rates without excessive wear.
Workpiece material The workpiece material also plays a significant role in determining the feed rate. Harder materials may require lower feed rates to prevent excessive tool wear, while softer materials can accommodate higher feed rates.
Machining operations Different machining operations have unique feed rate requirements. For instance, milling operations may need different feed rates than turning or drilling operations, depending on tool geometry and the specific CNC machining process.
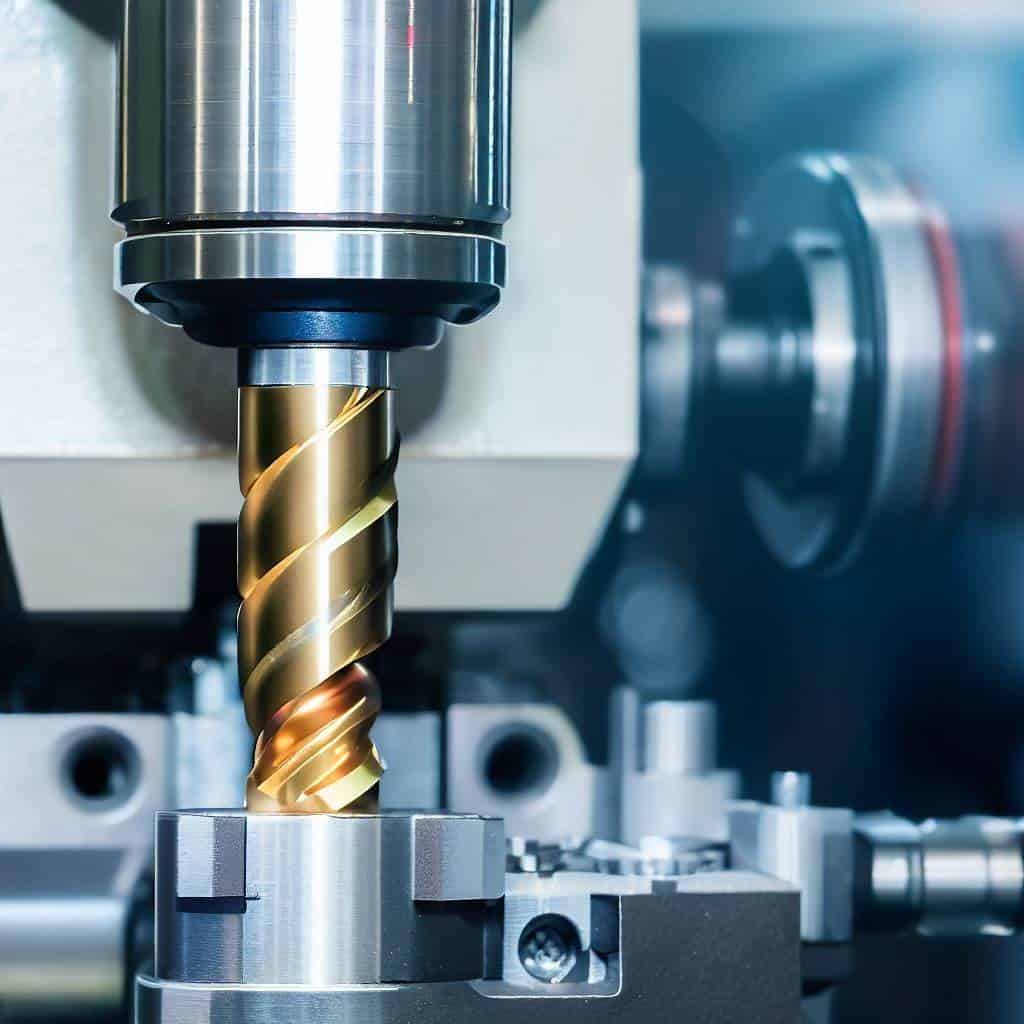
How to Calculate Feed Rate
The feed rate formula can be calculated using the formula:
Feed Rate = Chip Load x Number of Cutting Edges x Spindle Speed (RPM).
Chip load refers to the thickness of the material removed by each cutting edge during one spindle revolution, typically measured in inches or millimeters.
Feed rate on a CNC – In CNC machining, the feed rate is programmed into the machine’s control system, which then adjusts the cutting tool or workpiece movement accordingly. The CNC machine can adjust the feed rate based on cutting tool material, workpiece material, and machining operation.
RPM and feed rate – The spindle speed, measured in revolutions per minute (RPM), is directly related to the feed rate. A higher spindle speed typically requires a higher feed rate to maintain the desired chip load and ensure efficient material removal.
Feed rate in engineering – the feed rate is an essential parameter that affects the machining process’s efficiency, quality, and cost. Engineers must carefully consider factors such as cutting tool material, workpiece material, and machining operation when determining the appropriate feed rate for a specific application.
Understanding Cutting Speed
Definition of Cutting Speed
Cutting speed of a tool
Cutting speed, also known as surface speed, refers to the rate at which the cutting edge of a tool moves relative to the workpiece surface during a machining operation. It is typically measured in surface feet per minute (SFM) or meters per minute (m/min). Cutting speed is a crucial parameter influencing tool life, surface finish, and machining efficiency.
Cutting speed on CNC
In CNC machining, cutting speed is an essential parameter programmed into the machine’s control system. The CNC machine automatically adjusts the spindle speed (RPM) based on the desired cutting speed, considering factors such as cutting tool material, workpiece material, and machining operation.
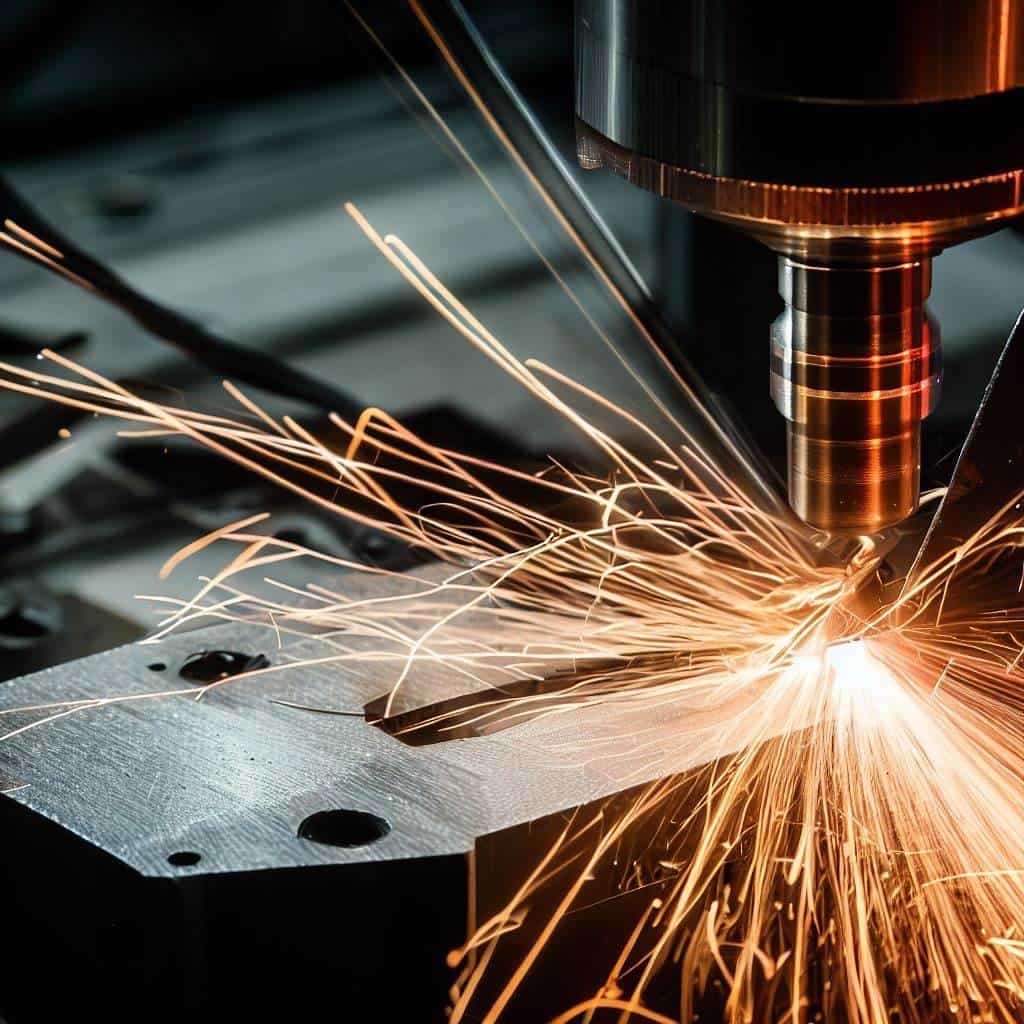
Importance of Cutting Speed
Cutting speed plays a significant role in the machining process. It directly affects tool life, surface finish, and material removal rate. A higher cutting speed can improve productivity and reduce machining time but may result in shorter tool life due to increased cutting temperature.
On the other hand, a lower cutting speed may extend tool life but can decrease productivity and increase machining time. Therefore, finding the optimum cutting speed that balances productivity, tool life, and surface finish is essential.
Factors Affecting Cutting Speed
The material of the cutting tool significantly impacts the cutting speed. Softer cutting tool materials, such as high-speed steel (HSS), generally require lower cutting speeds than harder materials like carbide or ceramic, which can withstand higher cutting speeds without excessive wear or heat generation.
2. Workpiece material
The workpiece material also influences the cutting speed. Harder materials usually require lower cutting speeds to prevent excessive tool wear and heat generation, while softer materials can accommodate higher cutting speeds.
3. Machining operations
Different machining operations have unique cutting speed requirements. For example, milling operations may require different cutting speeds than turning or drilling operations, depending on tool geometry, the specific CNC machining process, and the desired surface finish.

How to Calculate Cutting Speed
Understanding how to calculate cutting speed is crucial for optimizing machining operations, as it directly impacts factors such as tool life, surface finish, and material removal rate. The cutting speed is also known as surface speed and refers to the speed at which the cutting edge of a tool moves relative to the workpiece surface during a machining operation.
1. The formula for cutting speed
The formula for calculating cutting speed depends on whether you are working with imperial or metric units. In both cases, the cutting speed is determined by the diameter of the workpiece or cutter and the spindle speed (RPM). The formulas are as follows:
– For imperial units (surface feet per minute, SFM): Cutting Speed (SFM) = (Diameter (inches) x π x RPM) / 12
– For metric units (meters per minute, m/min): Cutting Speed (m/min) = (Diameter (mm) x π x RPM) / 1000
2. Surface speed in machining
Surface or cutting speed is an essential parameter in the machining process. It affects heat generation, tool life, and surface finish. The surface speed can be calculated using the above mentioned formulas, considering the workpiece’s diameter or the cutter’s spindle speed (RPM).
3. Surface speed measured
In Surface speed is typically measured in surface feet per minute (SFM) for imperial units or meters per minute (m/min) for metric units. These units describe the linear speed of the cutting edge of a tool relative to the workpiece surface during a machining operation.
4. Cutting speed vs. surface speed
Cutting speed and surface speed are synonymous terms in the context of machining. Both refer to the linear velocity of the cutting edge of a tool relative to the workpiece surface during a machining operation. The terms are often interchangeable and crucial for optimizing tool life, surface finish, and machining efficiency.
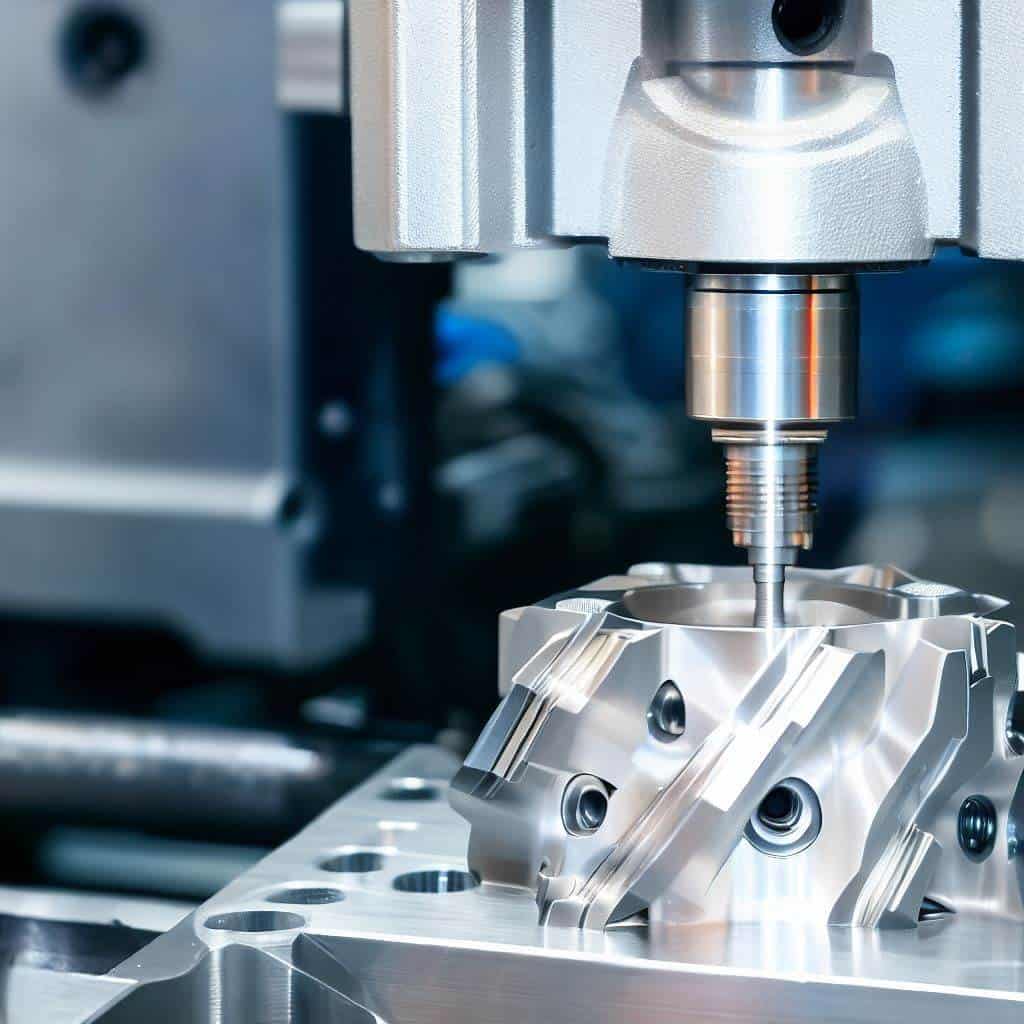
Cutting Speed vs. Feed Rate
Relationship between Cutting Speed and Feed Rate
Cutting speed and feed rate are interrelated parameters in the machining process. The cutting speed determines the rate at which the tool’s cutting edge moves relative to the workpiece, while the feed rate dictates the tool’s or workpiece’s linear motion during the operation.
Together, they significantly impact the material removal rate, surface finish, tool life, and machining efficiency. Balancing these two parameters is crucial for optimizing the machining process.
Difference between Cutting Speed and Feed Rate
The primary difference between cutting speed and feed rate lies in their definition and function within the machining process.
When machining, cutting speed refers to the cutting edge moving against the workpiece surface, and feed rate refers to the tool’s or workpiece’s linear motion. Cutting speed influences factors such as heat generation, tool life, and surface finish, while feed rate affects chip thickness, material removal rate, and tool wear.
How to Determine Optimum Cutting Speed and Feed Rate
1. Calculating surface speed
Surface speed (SFM) can be calculated using the formula: SFM = (Diameter of the workpiece or cutter x π x RPM) / 12 (for inches) or / 1000 (for millimeters), where RPM is the rotational speed of the spindle or workpiece.
2. Calculating SFM from rpm
To calculate the surface feet per minute (SFM) from spindle speed (RPM), use the formula: SFM = (Diameter of the workpiece or cutter x π x RPM) / 12 (for inches) or / 1000 (for millimeters).
3. Factors affecting optimum values
Several factors determine the optimum cutting speed and feed rate:
- Tool life: Increasing the cutting speed or feed rate may shorten tool life due to higher cutting temperature and wear. Conversely, decreasing these parameters may extend tool life but reduce productivity.
- Surface finish: Higher cutting speeds and lower feed rates usually result in a smoother surface finish. However, excessively high cutting speed may cause chatter and compromise the surface finish.
- Power consumption: Higher cutting speeds and feed rates may increase power consumption, increasing wear and tear on machine tools.
- Material removal rate: The cutting speed and feed rate directly affect the material removal rate (MRR). Higher values for both parameters can result in faster material removal but at the cost of increased tool wear and potentially reduced surface finish.
By considering these factors and using the appropriate formulas and guidelines provided by tool manufacturers or machining handbooks, machinists can determine the optimum cutting speed and feed rate for a specific operation.
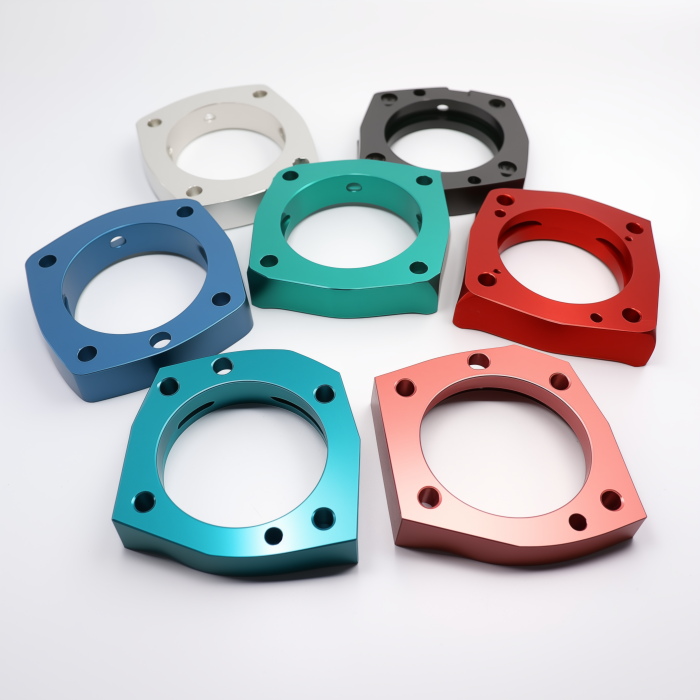
Common Questions and Misconceptions
Feed Rate and Cutting Speed in Different Machining Processes
1. Lathe operations
In lathe operations, the feed rate controls the linear motion of the cutting tool along the workpiece’s length. In contrast, the cutting speed depends on the workpiece’s rotational speed and diameter. Optimizing these parameters is crucial for achieving a high-quality surface finish, prolonging tool life, and ensuring efficient material removal.
2. Milling operations
In milling operations, the feed rate affects the cutting tool’s or workpiece’s linear motion, while the cutting speed affects the cutter’s rotational speed and diameter. Balancing the feed rate and cutting speed is essential for achieving the desired surface finish, minimizing tool wear, and maximizing machining efficiency.
3. CNC milling
In CNC milling, the feed rate and cutting speed are set into the machine’s control system, which adjusts the tool or workpiece movement accordingly. The CNC machine considers factors such as cutting tool material, workpiece material, and machining operation to determine the optimal feed rate and cutting speed.
Effects of Incorrect Feed Rate or Cutting Speed
1. Tool wear and tool life
An incorrect feed rate or cutting speed can significantly impact tool wear and life. Too high of a feed rate or cutting speed can cause excessive wear, resulting in shorter tool life, while too low of a feed rate or cutting speed may lead to inefficient material removal and increased tool cost.
2. Surface quality and surface roughness
Incorrect feed rate or cutting speed can also adversely affect the machined part’s surface quality and roughness. Higher cutting speeds and lower feed rates typically yield smoother surfaces, but excessively high cutting speeds may cause chatter and compromise surface finish.
3. Power consumption and efficiency
Inaccurate feed rates or cutting speeds can increase power consumption and reduce efficiency. Higher cutting speeds and feed rates demand more power and may cause wear and tear on the machine tools, while lower cutting speeds and feed rates may result in inefficient material removal and longer machining times.
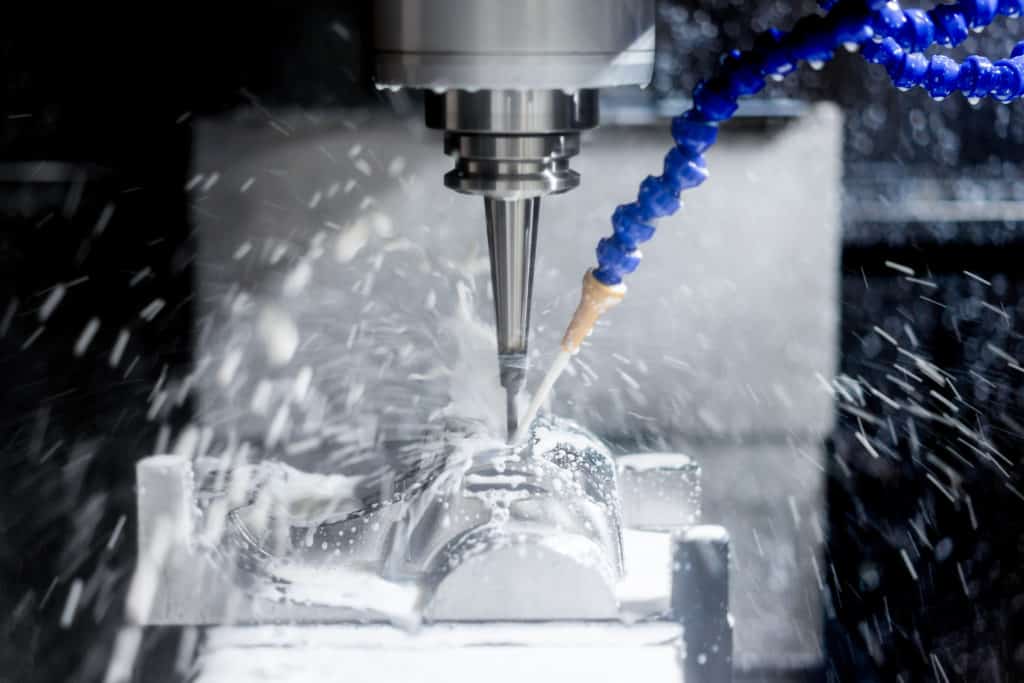
Choosing the Right Cutting Speed and Feed Rate
1. Factors to consider
Factors such as cutting tool material, workpiece material, machining operation, tool geometry, and desired surface finish are essential when selecting the appropriate cutting speed and feed rate. Specific CNC machining processes and machine tool capabilities may influence the optimal cutting speed and feed rate.
2. Tools and resources for calculations
Machinists can refer to guidelines provided by cutting tool manufacturers, machining handbooks, or software programs designed to assist in these calculations to determine the correct cutting speed and feed rate for a particular operation. These resources can help optimize the machining process, improve productivity, and prolong tool life while maintaining the desired surface finish and dimensional accuracy.
Conclusion
Cutting speed and feed rate are crucial factors in CNC machining that can significantly impact tool life, surface finish, and overall efficiency.
By understanding the relationship between these parameters, machinists can optimize their operations for better results. Incorporating the provided keywords and phrases into the article will help ensure a comprehensive understanding of these concepts, ultimately leading to more successful machining projects.
FAQS
Speeds and feeds refer to the cutting speed and feed rate parameters used in CNC machining. These parameters are crucial for optimizing machining efficiency, tool life, and surface finish. They are typically determined based on workpiece material, cutting tool material, and the specific machining operation.
The cutting parameters, including cutting speed and feed rate, directly impact the temperature generated during machining. Higher cutting temperatures can lead to accelerated tool wear and reduced tool life. Therefore, balancing cutting parameters to maintain a manageable temperature while achieving efficient material removal is essential.
Relative velocity refers to the speed at which the cutting edge of a tool moves relative to the workpiece during machining. It is essential in determining the cutting speed and affects factors such as surface finish, tool wear, and material removal rate.
Threading tools for creating workpiece threads require lower cutting speeds and feed rates than other cutting tools. This is due to the precise and intricate nature of the threading process, which demands more delicate machining parameters to achieve accurate thread profiles and maintain tool life.
Spindle speed, measured in RPM, is crucial in calculating cutting or surface speed. The spindle speed, along with the diameter of the workpiece or cutter, determines the linear rate of the cutting edge relative to the workpiece surface. Optimal spindle speeds help achieve the desired cutting speed, balancing tool life, surface finish, and machining efficiency.
Milling operations must balance cutting speed and feed rate to achieve efficient material removal, tool life, and surface finish. The primary difference is that milling involves the rotation of a cutter and the linear motion of the workpiece or cutter, which directly affects the cutting speed and feed rate calculations.
Factors such as the material of the workpiece, the hardness, the cutting force, the cutting temperature, and the tool geometry should be considered when working with an HSS cutting tool. HSS tools may require lower cutting speeds than carbide tools due to their lower thermal conductivity and tolerance for higher cutting temperatures.
Cutter diameter directly impacts cutting speed calculations, as larger diameters result in higher cutting speeds. The cut width, or radial depth of cut, affects the feed rate calculations, as it determines the amount of material the cutting tool engages during the machining process. Balancing the cutter diameter and cut width is essential for optimizing machining efficiency and maintaining tool life.
Factors such as workpiece material, cutting tool material, tool geometry, cutting force, chip thinning, and the subtractive manufacturing process should be considered when determining the optimum feed rate. Balancing these factors helps achieve efficient material removal, maintain tool life, and produce the desired surface finish.