Table of Contents
Copper
The Uniqueness of Pure Copper
Pure copper, often referred to as elemental copper, stands out in the world of metals. Copper is a type of metal with a unique reddish-brown color and a natural metallic form that is immediately usable.
It is popular for being very ductile, malleable, and has high thermal and electrical conductivity. Additionally, it is resistant to corrosion, making it an ideal material for many different uses.
Copper's Conductivity and Its Impact
Copper’s exceptional electrical and thermal conductivity traits have significantly shaped its applications. Its ability to conduct electricity efficiently makes it a preferred choice for electrical wiring, electrical terminals, and electric motors.
Its rapid heat transfer capability and excellent thermal conductivity make it a perfect fit for applications such as heat sinks, radiator cores, and heat exchangers. These properties and its corrosion resistance make copper versatile in various industrial applications.
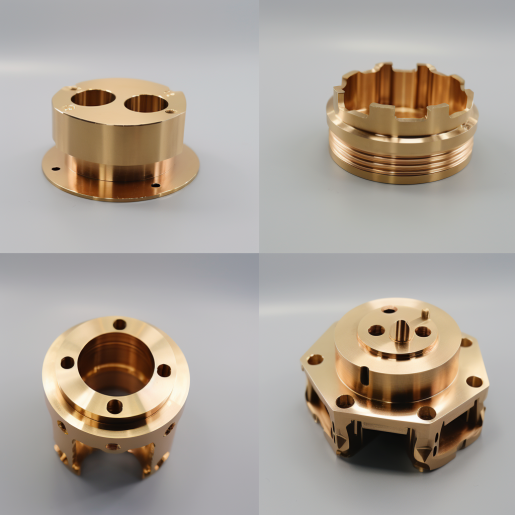
Brass
The Unique Characteristics of Brass Alloys
Brass, often recognized by its bright gold-like appearance, is an alloy primarily composed of copper and zinc. The proportion of these two elements can be varied to create a range of brasses with differing properties, making it a highly versatile material.
Unlike pure copper, brass alloys exhibit a higher degree of resistance to tarnishing and are generally harder and more resistant to corrosion. Adding other elements to the base copper material can further enhance the properties of brass, making it suitable for various applications, from musical instruments to water fittings and bolts.
When is Brass a More Suitable Choice Over Copper?
Brass tends to be a more suitable choice over copper in scenarios where higher malleability, low friction, and acoustic properties are required. For instance, brass is commonly used in the production of musical instruments due to its acoustic properties.
Its low friction makes it ideal for applications such as locks, gears, and doorknobs. Also, brass’s resistance to tarnishing and high corrosion resistance make it a popular choice for decorative components, jewelry, and applications in saltwater and sea environments.
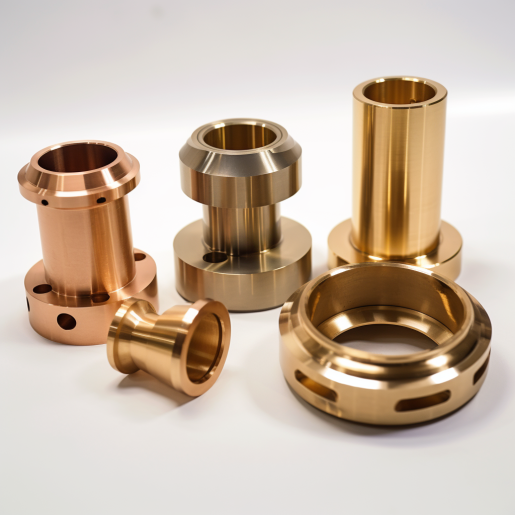
Bronze
Defining the Elemental Composition of Bronze
Bronze is another copper-based alloy, typically consisting of copper and tin. In addition to traditional bronze components, modern bronze alloys may contain aluminum, manganese, nickel, or zinc elements.
These variations are called aluminum bronze, manganese bronze, and so on. Adding these elements gives bronze its high strength and resistance to wear and corrosion, making it tougher than copper and brass.
Why Bronze Might Be the Preferred Choice in Certain Use Cases
There may be a preference for bronze over copper or brass in situations where strength, resistance to wear, and corrosion resistance are paramount.
For instance, bronze’s durability makes it an excellent choice for components in heavy machinery and automotive parts. Its resistance to corrosion by seawater makes it ideal for marine applications, such as the manufacture of ship propellers.
Bronze is also commonly used to produce statues and sculptures due to its attractive surface finish and superior metal casting characteristics. Its high-leaded tin bronze variant is particularly valued for its low friction properties.

Copper, Brass, or Bronze: Which Metal Reigns Supreme?
Each metal has unique strengths regarding the triumvirate of copper, brass, and bronze. Pure copper, renowned for its high electrical conductivity, is softer than brass and bronze. Copper is best suited for applications that require high electrical conductivity, like cathode ray tubes and electric motors.
On the other hand, brass and bronze are copper alloys with greater strength and durability, making them more suitable for heavy-duty applications. Brass, particularly, is known for its lustrous, gold-like appearance and exceptional corrosion resistance, especially in saltwater and sea environments. This makes brass, especially naval brass, popular for marine applications. The cost of brass varies depending on the type of brass (for example, yellow brass, cartridge brass, etc.) and the current scrap metal market.
Bronze, another copper alloy, is typically more expensive than copper and brass due to its strength and durability. Bronze’s resistance to wear and corrosion makes it a preferred choice for heavy-duty applications such as valve bodies and pipe fittings.
Metal | Strength | Cost | Corrosion Resistance |
Copper | Soft, easy to shape and manipulate | Typically more expensive than both bronze and brass | Moderate, develops a green patina over time |
Bronze | Hardest among the three, highly durable | expensive than brass | High, excellent resistance to wear and corrosion |
Brass | Harder than copper, varies depending on the type of brass | cheapest among copper and bronze. | High, especially in saltwater and sea environments |
Influencing Factors in the Selection of Copper, Brass, or Bronze
The selection between copper, brass, or bronze often hinges on the application’s specific requirements. Factors such as the need for electrical or thermal conductivity, corrosion resistance, strength, cost, and even aesthetic considerations can influence the choice.
For instance, the green patina that develops on copper and bronze might be desirable in certain decorative applications. At the same time, the bright, gold-like color of brass might be preferred by others.
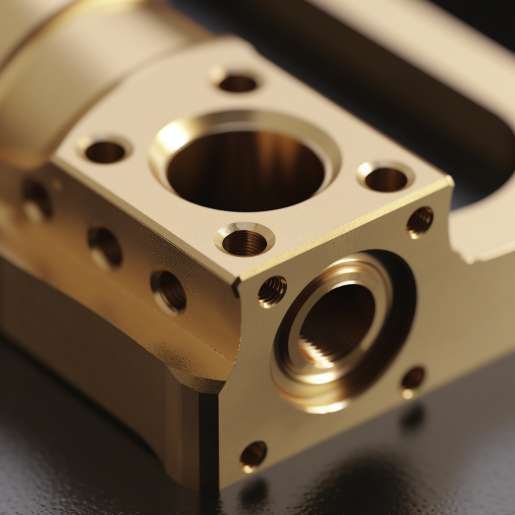
Deciphering the Differences: Copper, Brass, and Bronze
Identifying Based on Key Physical Properties
Copper, brass, and bronze can be distinguished based on physical properties. Copper is a metal commonly used in its pure state or as an alloy component, in addition to its unique reddish-brown color and high electricity and heat conductivity. It’s softer than brass and bronze, making it easy to shape and manipulate.
The metal alloy called brass consists primarily of copper and zinc. It is typically harder than pure copper and has a shiny, golden appearance. Zinc in brass gives it a higher melting point than pure copper, making it versatile for various applications, from musical instruments to water fittings and bolts.
Bronze is an alloy made up of copper and tin, but it may also contain additional elements such as aluminum, manganese, nickel, or zinc in modern times. Bronze is harder than copper and brass and has a higher melting point. This material is highly durable and resistant to wear and corrosion, making it the best option for heavy-duty applications.
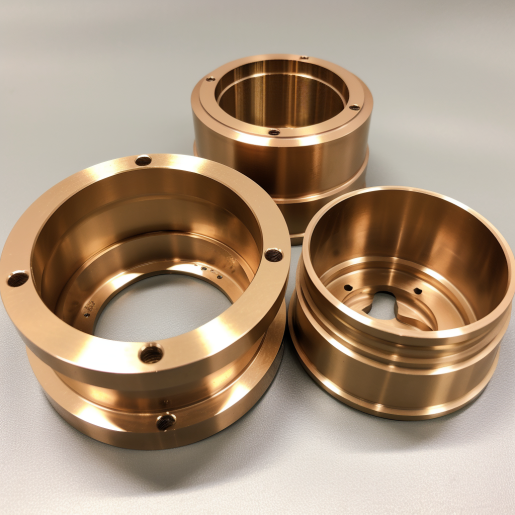
Differentiating Based on Color and Hardness
The color and hardness of these metals can also help in their identification. Copper has a distinctive reddish-brown appearance and is the softest of the three metals.
Brass is harder than copper and has a bright, gold-like color. Bronze, the hardest of the three metals, typically has a darker, more muted color than brass. These differences in color and hardness can be key in distinguishing between these three metals in various applications.
Metal | Color | Hardness | Key Applications |
Copper | Reddish-brown | Soft | Electrical wiring, radiator cores, electric motors |
Brass | Bright, gold-like | Harder than copper | Musical instruments, water fittings, bolts |
Bronze | Darker, more muted than brass | Hardest among the three | Valve bodies, pipe fittings, heavy-duty machinery components |
Wrapping Up
Understanding the nuances between copper, brass, and bronze is pivotal in engineering. Copper, a pure metal known for its high electrical and thermal conductivity, is ideal for applications like electric motors and heat exchangers. Its softness makes it easy to shape, unlike brass, a harder copper-zinc alloy.
Brass, available in various ranges like cast brass and soft brass alloy, excels in applications requiring corrosion resistance and durability. Its unique color and properties make it popular for decorative fasteners, water fittings, and musical instruments like clock brass.
Bronze, the toughest among the three, is the preferred choice for heavy-duty applications. Its durability and resistance to wear make it ideal for valve bodies and pipe fittings. Although a copper-based alloy, bronze’s element composition gives it unique properties that set it apart.
Whether copper vs. brass or brass vs. bronze, each metal has unique strengths and applications. Understanding these differences allows engineers to select the most suitable material, optimizing performance, longevity, and cost-efficiency.
Copper | Brass | Bronze | |
Color | Reddish-brown | Bright, gold-like | Darker, more muted than brass |
Hardness | Soft | Harder than copper | Hardest among the three |
Electrical Conductivity | High | Lower than copper | Lower than copper and brass |
Thermal Conductivity | High | Lower than copper | Lower than copper and brass |
Corrosion Resistance | Moderate | High, especially in saltwater and sea environments | High |
Key Applications | Electrical wiring, radiator cores, electric motors | Marine applications, musical instruments, decorative components | Valve bodies, pipe fittings, heavy-duty machinery components |
Frequently Asked Questions
Copper is a pure base metal with high conductivity and antimicrobial properties, commonly used in applications such as electric motors and water fittings. On the other hand, brass is an alloy mainly of copper and zinc, known for its durability, machinability, and decorative appeal.
Unlike copper, brass is an alloy whose properties can be manipulated by changing the proportions of copper and zinc. Its properties can range from soft to hard brass alloys.
Oxygen-free copper is a type of copper that has been refined to reduce the oxygen level to .001% or below. Its high electrical conductivity makes it highly desirable for applications like audio equipment, high-performance computers, and other electronics.
Both copper and brass are good conductors of heat. However, copper generally conducts heat better due to its pure element composition.
Bronze generally has higher durability and corrosion resistance than brass. This is why bronze is often used in applications that require resistance to wear, such as in bearings, clips, electrical connectors, and springs.
Copper has a reddish-brown color, brass has a yellowish color due to zinc, and bronze has a much darker brown color.
Yes, it’s called free-cutting brass. It contains additional amounts of lead to make it easier to machine.
Copper and its alloys, including brass, have been found to possess antimicrobial properties. That’s why they are often used on high-touch surfaces to prevent the spread of bacteria and viruses.
Brass is highly corrosion-resistant, malleable, and has an appealing yellow-gold color. This makes it popular for crafting decorative pieces, clocks, and fasteners.
Copper has a higher tensile strength than brass. Adding elements like iron or manganese to brass can also enhance its strength.
Arsenic brass is used for its improved corrosion resistance, especially in seawater. Gilding metal, a type of brass with high copper content, is used for decorative purposes due to its gold-like appearance.
Yes, both copper and brass have many commercial applications, such as in the manufacture of containers, heat exchangers, valves, pipes, locks, cartridge castings, and many more.