Hey there! Ready to figure out the best way to weld stainless steel? We will closely examine MIG and TIG welding and see which one nails it with precision strength and efficiently does the job. Let’s find out which one suits your projects best!
TIG welding is usually your best option for stainless steel. It’s awesome for getting those precise, clean welds, especially on thinner stuff. But hey, if you’ve got thicker material, MIG welding might be your faster, more efficient buddy.
Stick around as we dig into the nitty-gritty of MIG vs. TIG welding for stainless steel. We’ll help you sort out which one’s the better fit for your work based on what you need to get done.
Table of Contents
MIG vs. TIG Welding: Understanding the Basics
Choosing between MIG and TIG welding is crucial when tackling stainless steel welds. Each method brings strengths to stainless steel welding, whether working with austenitic stainless steel or other stainless steel grades.
Basic Process of MIG and TIG Welding
MIG (Metal Inert Gas) Welding: MIG welding, a form of gas metal arc welding, is about speed and efficiency, especially when welding stainless to mild steel or tackling thicker materials. It involves feeding a wire electrode – often a stainless steel wire – through a welding gun. This wire serves as the filler metal, melting into the weld joint. Shielded by a mix of inert gas like argon and active gases like carbon dioxide, MIG helps prevent oxidation and ensures successful welding with reduced corrosion resistance.
TIG (Tungsten Inert Gas) Welding: TIG welding, or gas tungsten arc welding, is more about precision, particularly suitable for thinner materials or when welding stainless steel that requires a high-quality finish. Using a non-consumable tungsten electrode, TIG allows for more control over the weld. The process often involves a filler material, with argon gas commonly used as the shielding gas to protect the weld zone and prevent hot cracking.
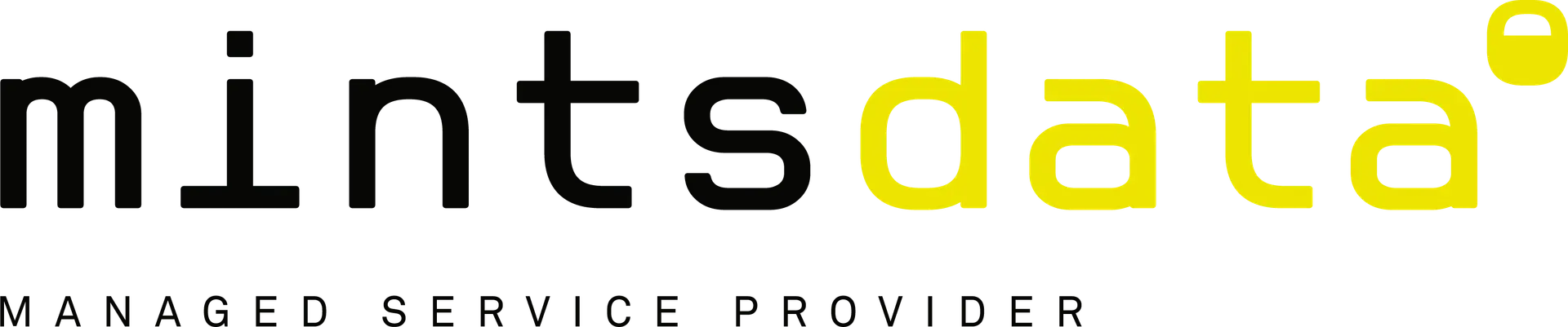
Discussing Advantages and Limitations
MIG Welding Advantages: Ideal for a range of stainless steels, MIG is great for projects requiring quick welds over large areas or thick materials. It’s effective in welding mild steel and different metals, offering versatility.
MIG Welding Limitations: It might struggle with very thin metals and requires careful heat input to prevent warping and maintain mechanical properties.
TIG Welding Advantages: TIG excels in welding stainless steel, especially for delicate work on thinner materials. The controlled heat input and cooling process produces a high-quality, clean weld with excellent corrosion resistance.
TIG Welding Limitations: TIG requires more skill and is slower, making it less ideal for larger projects or when speed is essential. It also demands specialized equipment, like TIG welding machines.

Types of Projects Best Suited for MIG and TIG
MIG for the Win: Choose MIG for general fabrication, automotive repairs, or when welding stainless steel to mild steel. It suits projects with less critical weld appearance, but speed and filler metal deposition are key.
TIG Takes the Crown: TIG is the preferred choice for precision tasks, such as in the aerospace industry, custom fabrication, or when working on stainless steel grades that require a clean finish. The chrome oxide layer is ideal for thermal expansion, and preventing carbide precipitation is crucial
Precision and Control in TIG Welding
TIG (Tungsten Inert Gas) welding, a staple in stainless steel welding, excels in precision and is ideal for tasks requiring a high level of detail on stainless steel, including austenitic stainless steel. This method is about control over the welding process, perfect for delicate stainless steel components where too much heat can cause warping or hot cracks.
By using a non-consumable tungsten electrode and a separate filler metal, TIG welding allows for adjusting heat input precisely, which is crucial for maintaining the mechanical properties of the base metal. The protective oxide layer formed during this slow cooling process ensures the integrity and corrosion resistance of the weld. Consequently, this makes TIG welding excellent for welding stainless steel to mild steel or other dissimilar metals, where precise thermal expansion control is necessary.

Efficiency and Speed with MIG Welding
MIG (Metal Inert Gas) welding is about efficiency and speed, especially when welding thicker stainless or mild steel materials. With continuous wire feeds as weld metal, this welding method significantly speeds up the welding process. Using carbon dioxide as part of the shielding gas mix in MIG welding helps achieve deeper penetration on thick materials, making it a robust welding method for heavy-duty stainless steel applications.
MIG welding’s ability to quickly join larger and thicker sections of stainless and carbon steel makes it a preferred choice for projects where time is a constraint. This process ensures successful welding even under high heat conditions, and the finished weld is strong and durable, suitable for both stainless steel and mild steel welding.
Material Thickness and Welding Choice
The decision between MIG and TIG welding often comes down to the material thickness and the specific type of stainless steel. TIG welding’s low heat input for thinner materials is ideal, preventing the risk of burn-through and ensuring a good weld with high corrosion resistance. It’s particularly suited for precision work on thinner stainless steel grades, where heat control is paramount.
Conversely, when welding thicker stainless steel or joining stainless to mild steel, MIG welding’s higher heat input and robust filler metal delivery make it more suitable. It effectively handles the thermal expansion and mechanical stress of welding thicker materials. MIG’s efficiency is advantageous in constructing welded joints in industrial applications, where speed and the ability to manage high temperatures are critical.
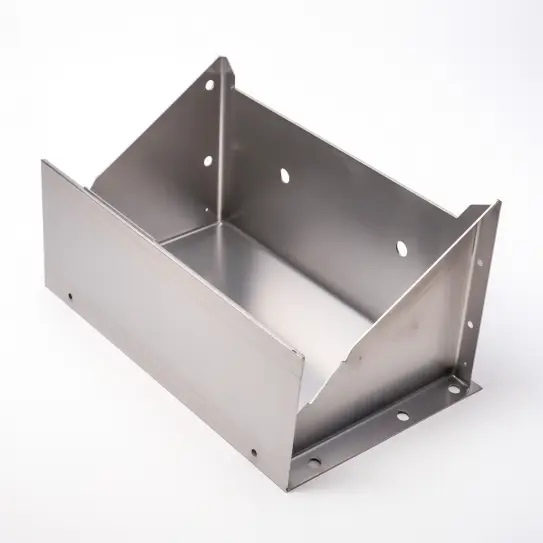
Choosing the Right Welding Technique
When it comes to welding stainless steel, the choice between MIG and TIG welding can make all the difference in your project’s success. Understanding the welding process and how these techniques interact with stainless steel, mild steel, and other metals is crucial for achieving the best results.
Project Complexity and Weld Quality
In projects involving austenitic stainless steel or other specialized alloys, TIG welding’s precision plays a key role. This method lets you carefully control the weld joint’s heat input and alloy composition, ensuring the stainless steel’s structural integrity and corrosion resistance. TIG is especially suitable for welding thin materials where precision is crucial, and the heat-affected zone needs to remain small.
MIG welding, which can lay down metal quickly using a variety of wire diameters, is ideal for projects where speed is more important than intricate detailing. This method is effective for welding stainless steel to mild steel and handling thicker materials, where the filler metal needs to penetrate the base metal adequately.

Production Speed and Efficiency
For large-scale or high-volume projects, the efficiency of MIG welding makes it a favorable choice. Its fast welding process and ability to handle electrical current efficiently ensure successful welding even on tougher materials. The use of shielding gas in MIG helps maintain the integrity of the weld, especially when dealing with a mix of stainless and carbon steel.
TIG welding, though slower, provides a high level of control over the welded joint, making it ideal for projects requiring a high-quality finish on stainless steel. Its ability to weld at lower temperatures helps maintain the metal’s mechanical properties and thermal conductivity, ensuring a durable and corrosion-resistant finish.
Balancing Factors for the Ideal Choice
Deciding between MIG and TIG welding involves considering the nature of your project, the types of metals involved, and the desired weld quality. A professional welder will assess factors like wire diameters, the composition of the filler metal, and the appropriate welding methods to ensure the strength and appearance of the weld meet the project’s needs.
Whether you’re welding stainless steel, mild steel, or a combination of different metals, choosing the right welding method is about understanding the properties of the materials and the demands of your specific project. Both MIG and TIG welding have their strengths, and the key is to match these with the requirements of your stainless steel welding project.
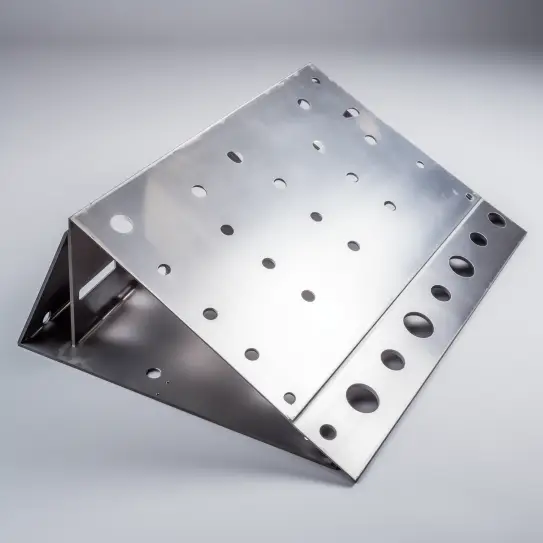
Factors to Consider When Choosing a Welding Method
Choosing between MIG and TIG welding methods for your stainless steel project involves several considerations:
Weld Quality: TIG welding excels in creating high-quality welds on stainless steel, crucial in projects demanding precision and corrosion resistance. The method allows fine control over the weld joint, making it ideal for stainless steel applications where appearance matters.
Project Size and Material Type: MIG welding is preferable for larger projects involving thicker materials, including welding stainless to mild steel. Its filler metal and shielding gas facilitate faster welding of two metals, making it efficient for extensive projects on the stainless steel side.
Welding Stainless and Mild Steel: MIG welding offers the versatility and speed needed for projects involving stainless and mild steel. Its ability to handle diverse base metals and weld mild steel effectively makes it a practical choice.
Heat-Affected Zone and Material Properties: TIG welding is more appropriate for projects where maintaining thermal conductivity and minimizing the heat-affected zone in stainless steel are crucial. This method ensures the integrity of the base metal, which is especially important in precision applications.
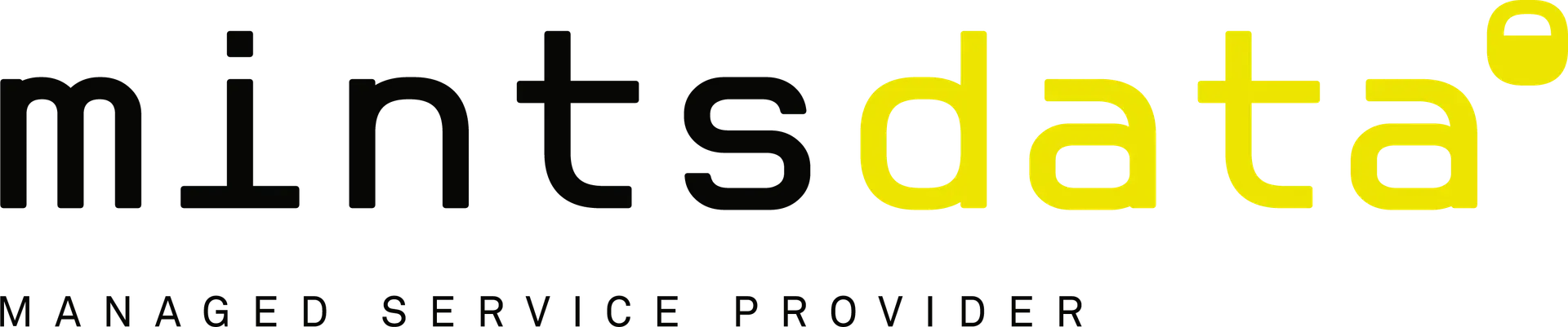
Practical Applications
Real-world examples of MIG and TIG welding highlight their distinct advantages:
MIG Welding Applications: MIG welding is often used in construction and automotive industries, especially for projects that require welding stainless steel to mild or carbon steel. Its efficiency in creating strong weld joints on thicker materials makes it suitable for large-scale fabrications, where proper welding procedures and speed are key factors.
TIG Welding Applications: TIG welding is the method of choice in scenarios requiring detailed work on stainless steel, such as custom fabrication or repair work where corrosion resistance and weld quality are paramount. This technique is particularly effective in maintaining the properties of the stainless steel, ensuring a high-quality finish with minimal chromium oxide formation at the weld.
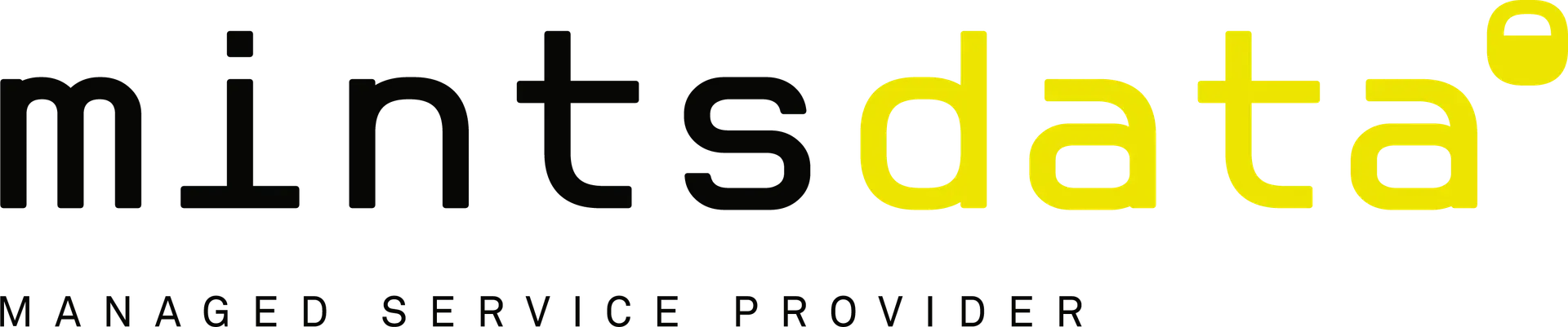
Conclusion
Deciding between TIG and MIG for welding stainless steel hinges on understanding each method’s strengths. TIG is precise in welding thinner stainless or mild steel, offering clean weld joints and excellent corrosion resistance. MIG welding, on the other hand, is the go-to for larger projects or when working with thicker materials like carbon steel, thanks to its efficient use of filler metal and ability to quickly produce strong welds
Connect with okdor
At Okdor, we specialize in custom parts manufacturing, including CNC machining, sheet metal fabrication, and progressive die stamping. Our expertise in these areas extends to providing top-notch welding solutions, whether your project calls for the detailed finesse of TIG or the robust power of MIG welding. For projects requiring the perfect combination of skill and technology in welding stainless, mild, or carbon steel, contact us at sales@okdor.com. Let’s work together to bring precision and quality to your custom parts needs.
Frequently Asked Questions
TIG welding is considered the best for welding stainless steel. It’s ideal for achieving precise weld joints and maintaining the integrity of the stainless steel, especially regarding chromium oxide preservation.
MIG welding is generally the easiest way to weld stainless steel, especially for those less experienced. It quickly joins the base metal and is suitable for various stainless and mild steel projects.
Welding stainless steel can be challenging due to its thermal conductivity and tendency to form chromium oxide, which requires careful heat management to prevent warping and maintain its corrosion resistance.
You can weld mild steel to stainless steel. This process typically involves using a suitable filler metal to ensure a strong bond and mitigate corrosion at the weld joint.
Using 308 filler metal is common for welding stainless steel to mild steel. Although corrosion resistance may vary, it helps create a stable weld joint between these two metals.
Metals like high-carbon steel and certain stainless steels are among the hardest to weld, often requiring specialized filler metals and stick welding or resistance welding techniques.
Welding stainless steel to raw (carbon) steel is possible, but it requires the right filler metal and welding techniques to ensure a reliable weld joint and to minimize corrosion.
Preparing stainless steel for welding involves cleaning to remove any oxides ensuring the base metal is free from contaminants. It’s also crucial to properly align and clamp the steel for a solid weld.
After welding, stainless steel can rust if the weld area lacks proper treatment or if the chromium oxide layer is compromised, reducing its natural corrosion resistance.
MIG welding stainless steel without a shielding gas is not advisable. The lack of gas can affect the weld quality and compromise the stainless steel’s corrosion resistance.