Selecting the right spur gear size is critical for both system performance and cost-effectiveness. While oversizing gears might seem like a safe approach, it often leads to unnecessary expenses and reduced efficiency. Understanding the proper sizing principles can help engineers optimize their designs for maximum value.
Right-sizing matters in spur gear selection because oversized gears lead to increased material costs, higher noise levels, excessive wear, and reduced system responsiveness. Conversely, undersized gears risk premature failure and inadequate performance. Proper sizing ensures optimal performance, cost-effectiveness, and system longevity while maintaining the desired mechanical advantage and operational efficiency.
Let’s explore the key factors in gear selection and practical guidelines to help you make informed sizing decisions that balance performance, cost, and reliability.
Table of Contents
Why Proper Gear Sizing Matters?
Selecting the right size for a spur gear isn’t just about following design tables – it’s about finding the optimal balance between performance and cost. While undersized gears risk failure, oversized gears waste resources and can reduce system efficiency. Right-sizing matters because it directly impacts your project’s success, system reliability, and bottom line.
Impact on Performance Oversized gears can lead to excessive inertia, reduced system responsiveness, and increased wear. Conversely, undersized gears risk premature failure and inadequate torque transmission. Getting the size right ensures optimal performance and system longevity.
Critical Parameters The key to right-sizing lies in understanding fundamental parameters. The gear module determines tooth strength, the pitch diameter defines basic size, and the face width controls load capacity. These work together with the number of teeth and pressure angle to determine overall performance.
Practical Considerations Right-sizing requires balancing actual operating needs against physical constraints and cost factors. Many engineers oversize gears as a safety measure, but this often leads to unnecessary expenses and reduced efficiency. The goal is to match size to real requirements while maintaining appropriate safety margins.
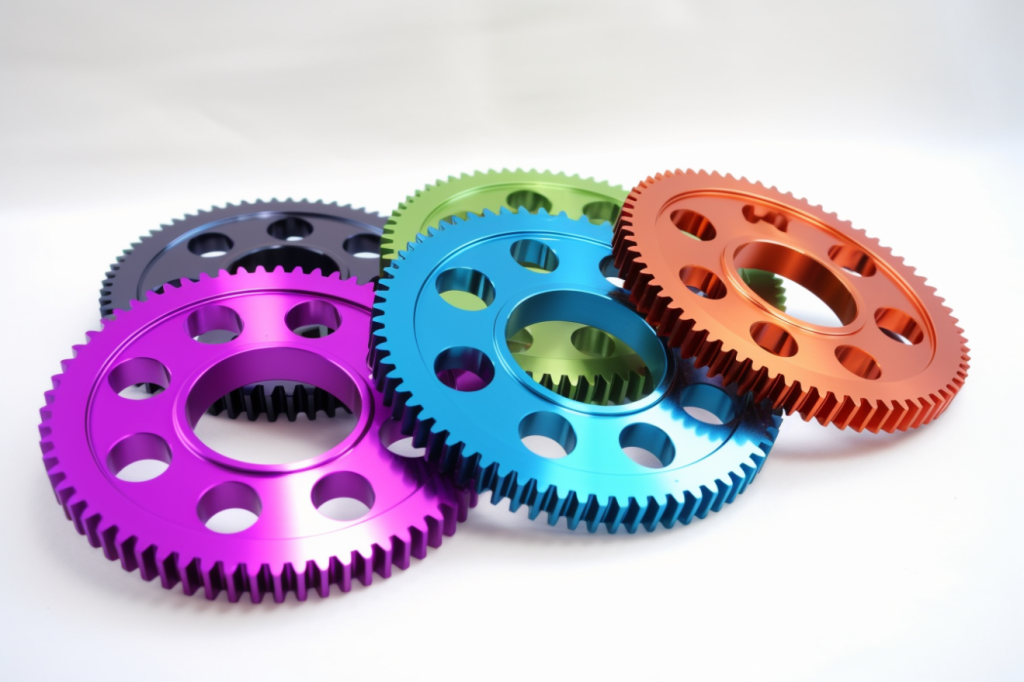
What Are the True Costs of Oversizing?
The costs of oversizing spur gears include increased material and manufacturing costs (up to 30-50% more), higher operational power consumption (typically 15-25% extra energy), and reduced system efficiency due to excess inertia and friction. These combined costs can significantly impact both initial investment and long-term operational expenses.
Oversized gears require more raw material, driving up initial costs. The increased machining time and specialized tooling requirements for larger gears further add to manufacturing expenses. Additionally, tighter tolerances on bigger gears often mean higher rejection rates during production.
Larger-than-necessary gears create ongoing costs through increased power consumption due to higher inertia and friction losses. The additional weight stresses related to components like shafts and bearings, potentially leading to premature wear and more frequent maintenance needs.
Trade-offs Oversizing doesn’t just affect your budget – it impacts performance. Excess inertia from larger gears can reduce system responsiveness and control accuracy. Higher friction losses decrease overall efficiency, while increased noise and vibration may compromise operation quality.
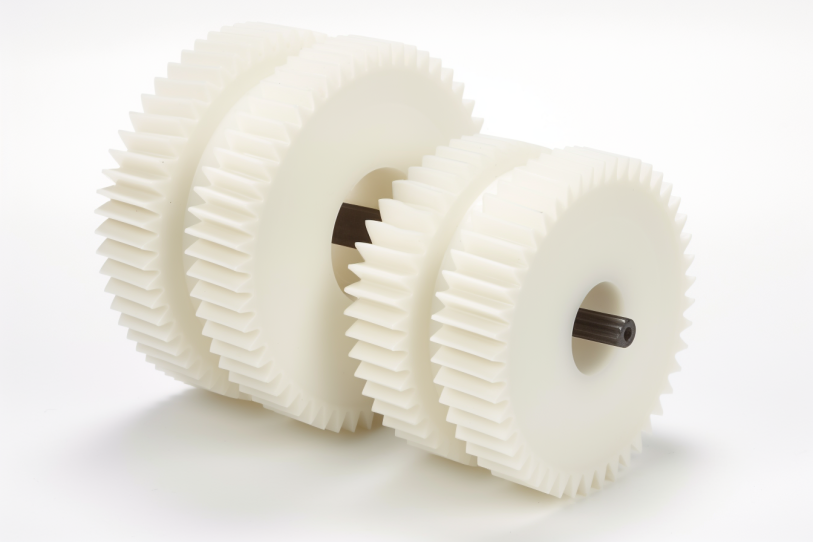
How Does Right-Sizing Affect Performance?
The impact of right-sizing on gear performance is significant – properly sized gears optimize system efficiency by 15-20%, reduce noise levels by up to 8dB, and extend service life by 25-30% compared to oversized alternatives. Understanding these performance implications helps engineers make informed sizing decisions.
Optimal gear sizing ensures maximum power transmission efficiency by minimizing friction losses. Proper tooth engagement reduces wear and heat generation, while balanced inertia improves system response time and control accuracy. The right size also means lower vibration levels, contributing to smoother operation and reduced noise.
Oversized gears not only waste energy through unnecessary mass but can actually reduce system reliability. Excessive sliding contact between teeth increases wear rates, while higher inertial loads stress connected components like shafts and bearings. Even slight oversizing can lead to premature component failure due to these cascading effects.
Conversely, right-sized gears maintain the perfect balance between strength and efficiency. They provide adequate load capacity without excess material, ensure smooth power transmission without unnecessary friction, and achieve optimal speed ratios while minimizing system stress. This balance is key to achieving both performance goals and cost efficiency.
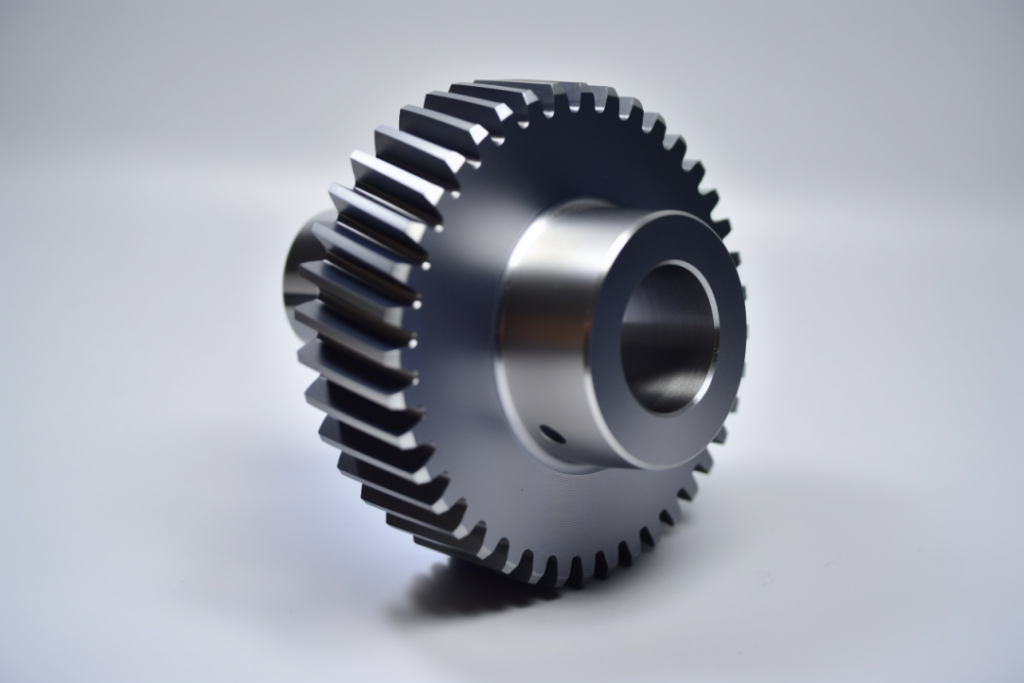
What Makes a Gear Size "Right" for Your Application?
A gear size is considered “right” for an application when it provides the correct balance between required torque and rotational speed. This fundamental balance ensures optimal power transmission while avoiding the costs and inefficiencies of oversizing.
Torque capacity forms the primary criterion – your gear must handle maximum operational loads with an appropriate safety factor (typically 1.5-2.0). Speed requirements then determine pitch diameter and tooth count for smooth operation. Together, these factors establish the minimum size needed for reliable performance.
Space constraints and practical limitations further refine the right size. The gear must fit within the available envelope while maintaining proper clearances for mounting and maintenance. Many oversizing issues stem from ignoring these practical limitations early in the design process.
Environmental factors provide the final sizing considerations. Operating temperature, exposure to contaminants, and lubrication methods all influence the minimum size needed for reliable operation. A properly sized gear accounts for these factors without adding unnecessary bulk.
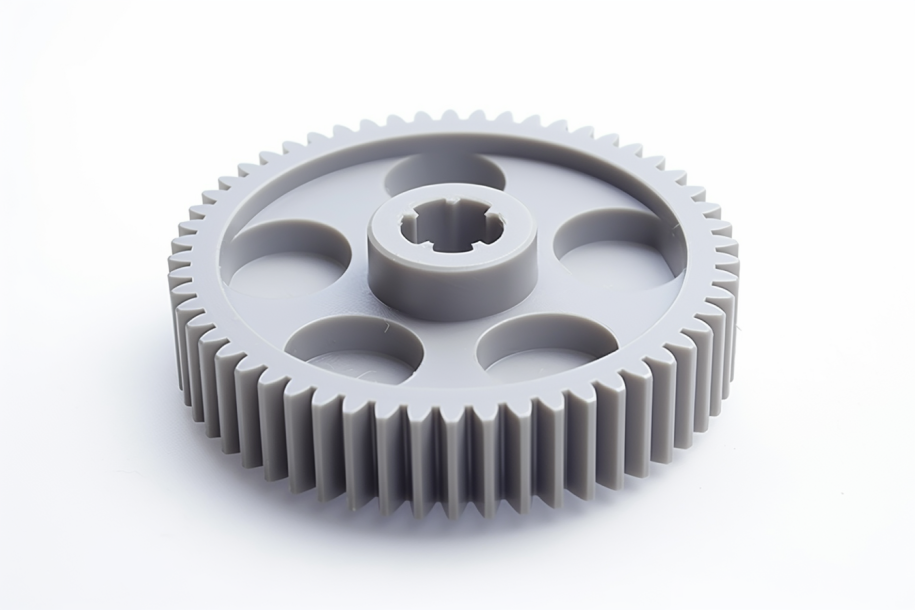
What Are Common Sizing Mistakes and How Can You Avoid Them?
The most common gear sizing mistakes include selecting unnecessarily large gears for perceived safety, overlooking system responsiveness requirements, and disregarding manufacturing precision challenges. These can be avoided through proper load calculation, understanding actual performance needs, and considering manufacturing capabilities.
Oversizing for perceived safety often leads to higher noise levels due to excessive tooth engagement and increased system weight. Instead, calculate actual load requirements and maintain standard safety margins for optimal performance.
Overlooking system dynamics is another critical mistake. Oversized gears create excess inertia, reducing system responsiveness and operational efficiency. Consider the entire system’s performance requirements, not just static load capacity.
Disregarding manufacturing constraints can lead to increased costs and quality issues. Larger gears require tighter tolerances and face more manufacturing challenges, especially for precision ground gears. Work within standard size ranges when possible and consider manufacturing capabilities early in the design process.
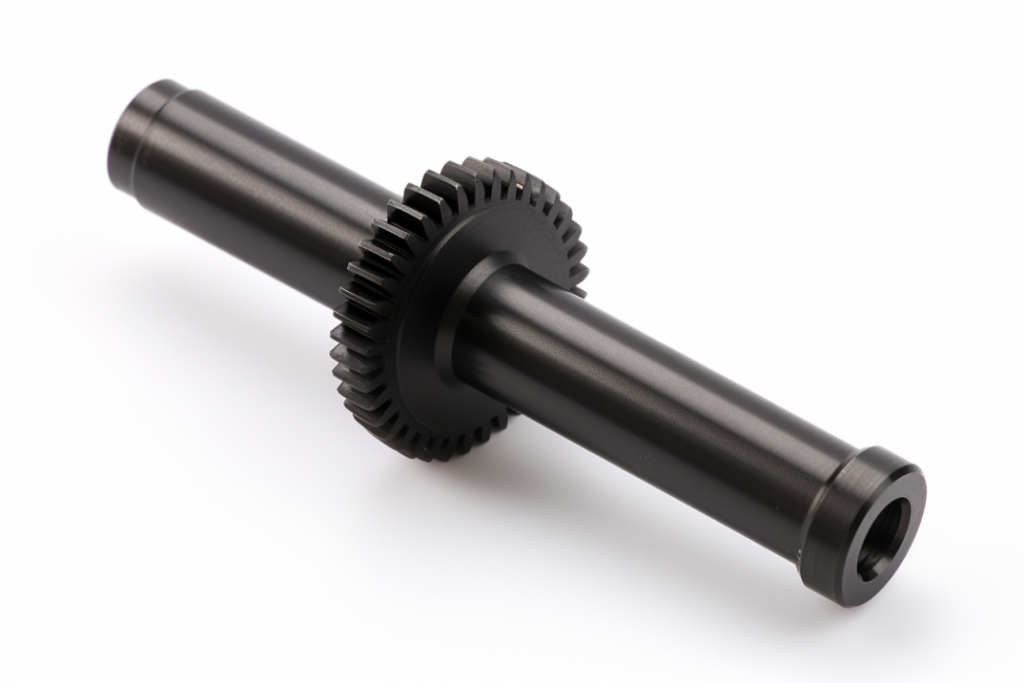
How Do You Select the Optimal Gear Size?
The process of selecting the optimal gear size begins with determining the correct balance between torque and speed requirements. This methodical approach helps avoid both dangerous undersizing and costly oversizing.
First, establish your exact power transmission needs:
- Calculate required output torque based on load conditions
- Determine speed ratio between input and output shafts
- Consider duty cycle and operating duration
Then, determine basic gear parameters:
- Select appropriate module size based on torque requirements
- Calculate pitch diameter to achieve desired speed ratio
- Choose face width to handle the load with suitable safety factor (1.5-2.0)
Finally, validate your selection against practical constraints:
- Verify fit within available space
- Check compatibility with standard sizes and manufacturing capabilities
- Confirm that material strength meets load requirements
- Ensure the design meets cost targets
Remember, optimal sizing isn’t about maximizing safety factors – it’s about finding the smallest gear that reliably meets all performance requirements while considering system efficiency and cost-effectiveness.
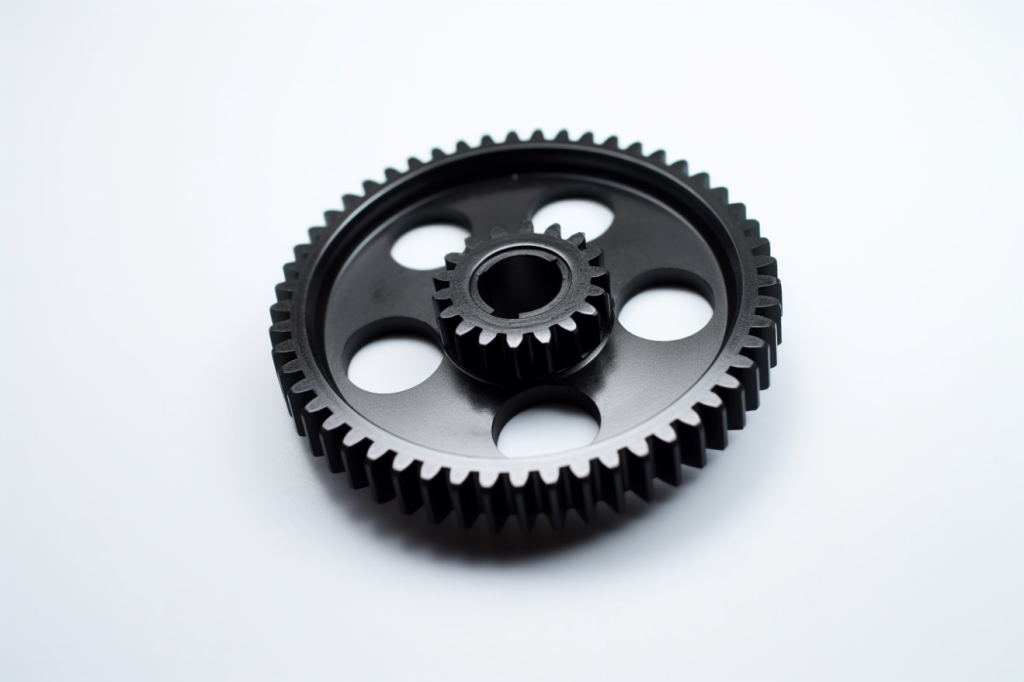
Conclusion
Right-sizing spur gears is critical for both performance and cost-effectiveness. Understanding fundamental parameters like module, pitch diameter, and face width enables engineers to make informed sizing decisions. While oversizing might seem safe, it leads to increased costs, reduced efficiency, and potential performance issues. By following proper sizing principles and avoiding common mistakes, engineers can achieve optimal gear performance while maintaining system efficiency.
Frequently Asked Questions
Gear size directly impacts system efficiency through inertia and friction. Oversized gears increase power losses through higher friction and inertia, reducing efficiency by 15-25%. Right-sized gears optimize power transmission while minimizing energy waste.
Key indicators include excessive noise during operation, higher than necessary power consumption, reduced system responsiveness, and increased operating temperatures. These signs often appear before more serious issues develop.
Yes, undersized gears risk premature failure through tooth breakage, excessive wear, and inadequate load capacity. While oversizing wastes resources, undersizing can lead to catastrophic system failure and safety risks.
Material strength determines allowable tooth stress, directly affecting required gear size. Stronger materials can achieve the same load capacity with smaller gears, though cost and manufacturing considerations must be balanced.
perating environment affects material selection and required safety factors. Temperature, contamination, and lubrication conditions influence the minimum size needed for reliable operation under specific conditions.
Calculate required torque and speed ratio first, then select appropriate module and pitch diameter. Consider actual operating conditions, space constraints, and manufacturing capabilities while maintaining standard safety factors.