Table of Contents
Understand Sheet Metal Properties
Achieving superb outcomes when working with sheet metal necessitates a complete comprehension of its properties and characteristics. Therefore, it is vital to contemplate the following essential factors:
- Gauge: Gauge dictates the thickness of sheet metal, with higher numbers denoting thinner sheets. Heavier gauges are notoriously difficult to cut or shape, whereas lighter gauges may be more flexible and susceptible to warping.
- Ductility: Possessing extraordinary malleability, sheet metal with high ductility can flex and contort without fracturing or rupturing. Through this remarkable strength, it can easily mold into various shapes and sizes.
- Corrosion resistance: When the project requires a sheet metal exposed to potentially damaging elements like moisture or corrosive material, selecting one with maximum corrosion resistance is critical. Doing so will guarantee your finished product lasts longer and demands less upkeep over time.
- Surface finish: A sheet metal’s surface can drastically influence its look and function. Polished, smooth finishes may be desired for visual purposes, whereas textured surfaces may improve grip or eradicate glares.
- Alloy composition: To guarantee that the finished product meets its specifications, choosing the appropriate alloy for sheet metal is essential, as each one holds unique properties, including strength, ductility, and corrosion resistance.
Considering these properties and characteristics, you can select the appropriate sheet metal for your project and ensure you can work with it effectively to achieve high-quality results.
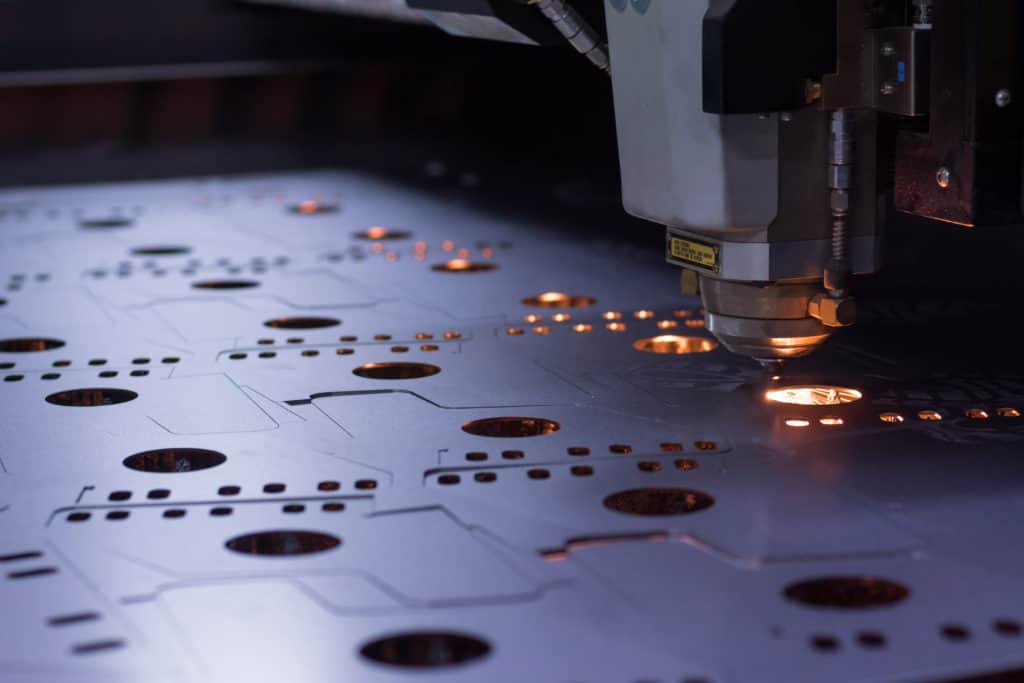
Materials Selection
Finding the ideal sheet metal for your task ensures you finish it with exceptional results. Selecting the suitable material for your project requires consideration of the following factors:
- Application: When selecting the best sheet metal properties for your product, consider what elements or weights it needs to withstand. Depending on whether it is subjected to weather extremes, hazardous chemicals, and/or substantial weight loads can affect its thickness, strength, and rust resistance. It would help if you determined these factors to make an informed decision when deciding which sheet metal is suitable for your application.
- Material cost: Beyond being mindful of the quality and versatility of sheet metal, its cost is an additional factor to consider due to the range in price stemming from different alloys and thicknesses.
- Availability: When evaluating the availability of sheet metals, determine if they are readily available from vendors or if you have to place a custom order.
- Fabrication requirements: Varying sheet metals may demand different fabrication approaches depending on their properties. For instance, some alloys are more amenable to cutting, forming, and welding than others.
- Aesthetic considerations: If the final product’s appearance is essential, consider the surface finish and color of the sheet metal.
With some thought and consideration, you can select the sheet metal that meets your project’s specifications and is easy to work with.
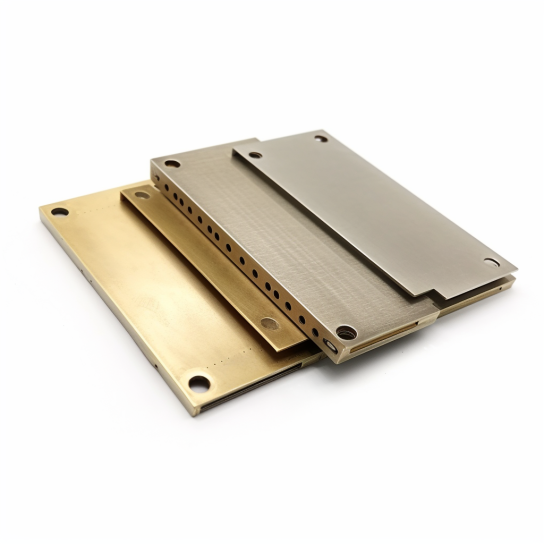
Tools Selection
Carefully selecting the right tools and equipment is essential to guarantee maximal efficiency and productivity when working with metal sheets. Here are a few points to remember as you make your decision:
- Cutting tools: You must select a suitable tool for the sheet metal’s thickness. Possible choices include aviation snips, shears, nibblers, and plasma cutters; make sure your option is compatible with the type and thickness of sheet metal.
- Forming tools: The size and thickness of sheet metal should be carefully considered when selecting a device such as a brake, roller, or press. Every piece has unique characteristics crucial to creating the perfect bend or shape. With the proper tools, you can masterfully craft any design imaginable!
- Welding equipment: Select the ideal approach and equipment when welding is necessary. TIG, MIG, and stick welding are all excellent choices—each with its own set of benefits and restrictions—so make your choice based on the sheet metal alloy’s requirements in terms of thickness.
- Safety equipment: Sheet metal work can be hazardous, so proper safety gear is paramount. Always wear gloves, protective eyewear, ear plugs or muffs for noise control, and a respirator to protect yourself from injury and fumes.
- Measurement tools: Precision is a must when dealing with sheet metal. To guarantee exact cuts and bends, use tools like rulers, calipers, and angle finders for accurate measurement.
Choosing the right tools and equipment can help you work with sheet metal more productively, reducing mistakes while ensuring top-notch results.
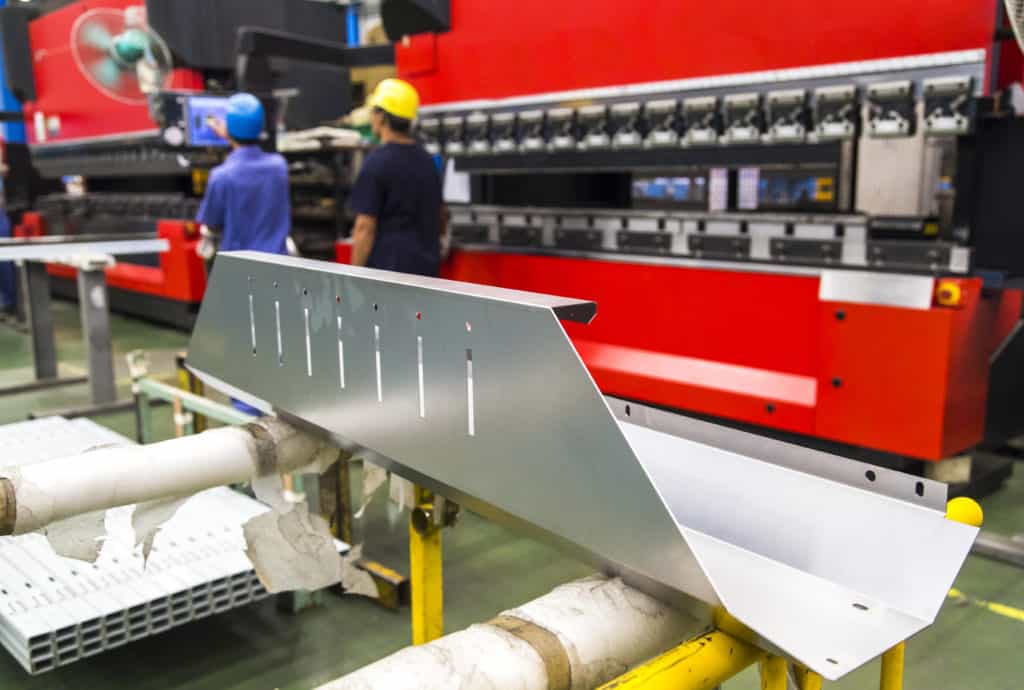
Cutting Sheet Metal Accurately
Achieving exactitude with sheet metal is vital to producing a product that meets the desired specifications and exceeds quality standards. To ensure accuracy, consider these helpful tips when cutting:
- Measure twice, cut once: Precision is paramount when dealing with sheet metal. Before making any cuts, always double-check your measurements to ensure accuracy.
- Use a straight edge: Utilizing a straight edge like a ruler or square will ensure that you make precise and balanced cuts.
- Mark the cut line: Utilize a marker or scribe to indicate the cut line on your sheet metal for easily visible and accurate results.
- Choose the appropriate cutting tool: The right cutting tool is essential for achieving your desired cut in sheet metal of varying thickness and type. Assess the material you’re working with before picking a suitable tool to get you excellent results.
- Cut slowly: Haste makes waste, so go slow to ensure neat and accurate cuts. Avoiding quick snips will help you achieve a uniform cut with smooth edges. Take your time for the best results!
- Consider the kerf: When determining the measurements required for a cut, it is essential to remember the kerf. The kerf refers to the width of material removed by a saw blade or cutting tool; when considering this, you can ensure that your end product will be precise in size.
- Use a deburring tool: To ensure your final product is flawless and safe, use a deburring tool to smooth any sharp edges or burrs left behind after cutting.
You can accurately measure and cut sheet metal pieces by strictly following these steps. This way, your final product can adhere to the quality standards it needs while also achieving the required specifications.
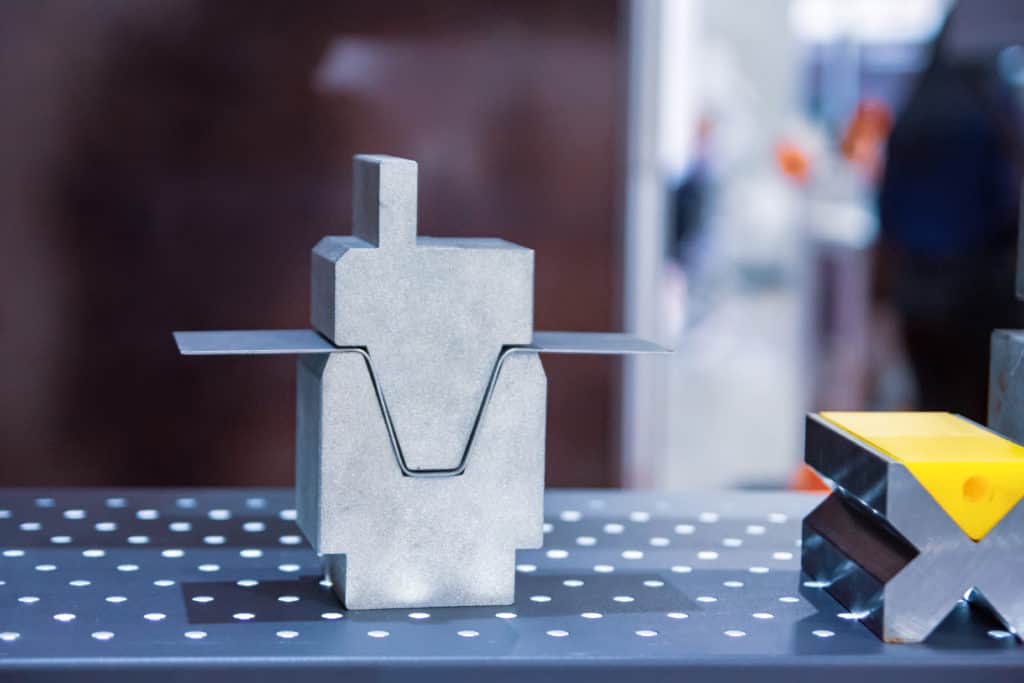
Control Shaping Process
From products to parts, forming, bending, and shaping sheet metal offers many valuable applications—but only when done correctly. To ensure success in your projects, here are some expert tips for achieving accurate and high-quality results:
- Choose the appropriate forming tool: Depending on the bend or shape you want to create, various forming devices, such as brakes, rollers, and presses, should be selected astutely to produce the desired outcome.
- Thickness and type of sheet metal: Forming thicker metal may require extra strength or a specialized tool to accomplish the desired bend and shape. Additionally, different types of metals have varying levels of formability; thus, selecting an appropriate tool for whatever kind of metal you use is vital.
- Use a back gauge: A back gauge guarantees that your sheet metal bends are even and consistent throughout.
- Bend in stages: To attain intricate curves and shapes, bending the sheet metal in successive steps may be essential using diverse forming processes or tools.
- Use a mallet or hammer: A mallet or hammer can delicately sculpt the sheet metal for minor shifts or modifications.
- Consider the spring back: When forming sheet metal, remember that it may spring back slightly after bending or shaping; when measuring and creating the item, account for this phenomenon to guarantee that your final product fulfills its purpose.
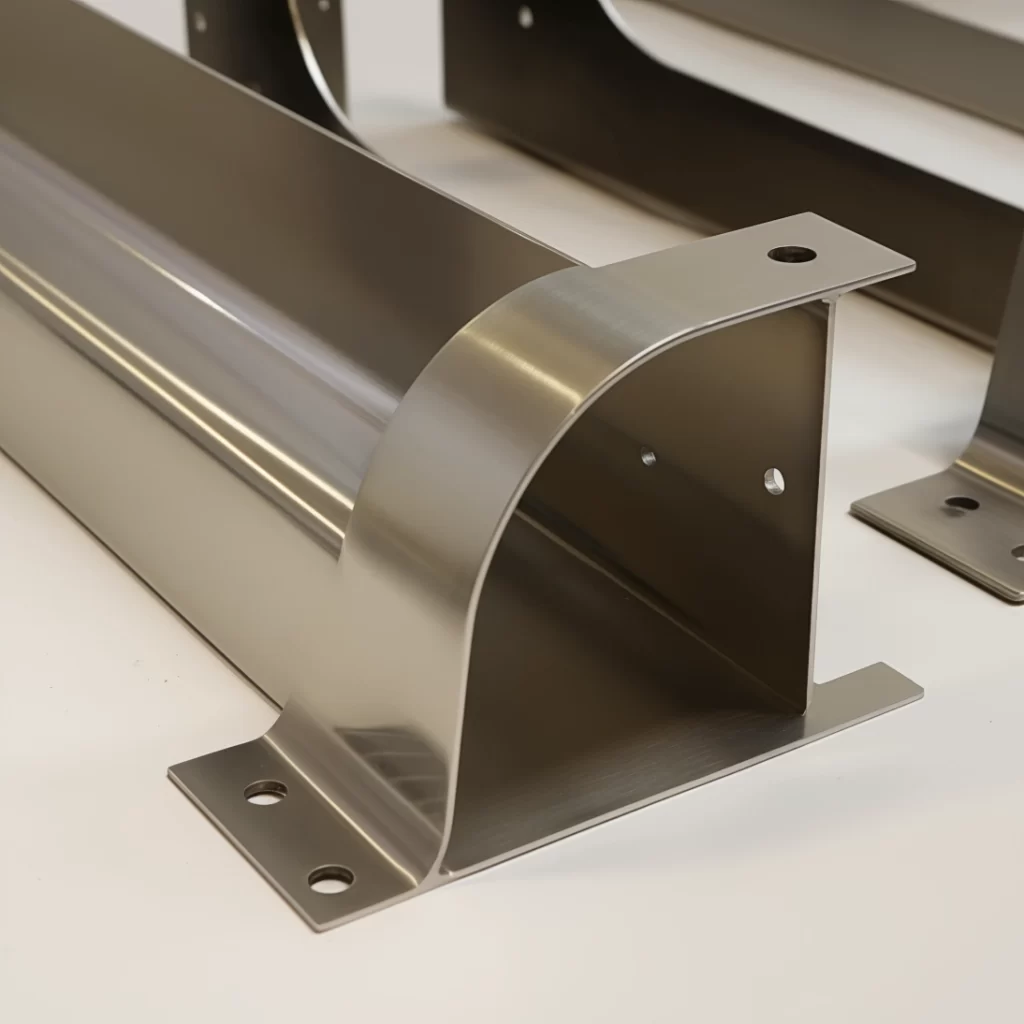
Welding and Joining
It is essential to properly weld and connect metal components to create products that deliver lasting quality and strength. To secure successful welds each time, employ these steps:
- Welding method: Select a suitable welding method for your material to achieve the highest quality welds. Options such as TIG, MIG, and stick welding could be available; decide on one that best meets your project needs.
- Prepare the surfaces: Before welding, ensure the covers are spotless and prepped correctly. A clean surface will provide a good connection by eradicating any dirt, corrosion, or contaminants that may influence the weld’s quality.
- Filler material: To ensure a robust and enduring joint, the filler material used for welding must be suitable for the sheet metal welded.
- Control heat input: Warped and altered metal is often the result of excessive heat. Thus, to successfully weld using a flame torch requires patience, aptitude, and exacting technique. Even minor discrepancies can lead to disastrous results, so always have the correct settings before starting any welding project!
- Ensure proper fit-up: Securing the pieces you’re welding together is essential for a reliable, enduring joint. Use clamps or other fixtures to keep them in place as you weld.
- Welding technique: Follow proper welding techniques, such as maintaining a consistent travel speed and angle, to ensure a high-quality weld.
- Inspect the weld: After welding, check the weld to ensure it looks good. Fix anything that needs fixing.
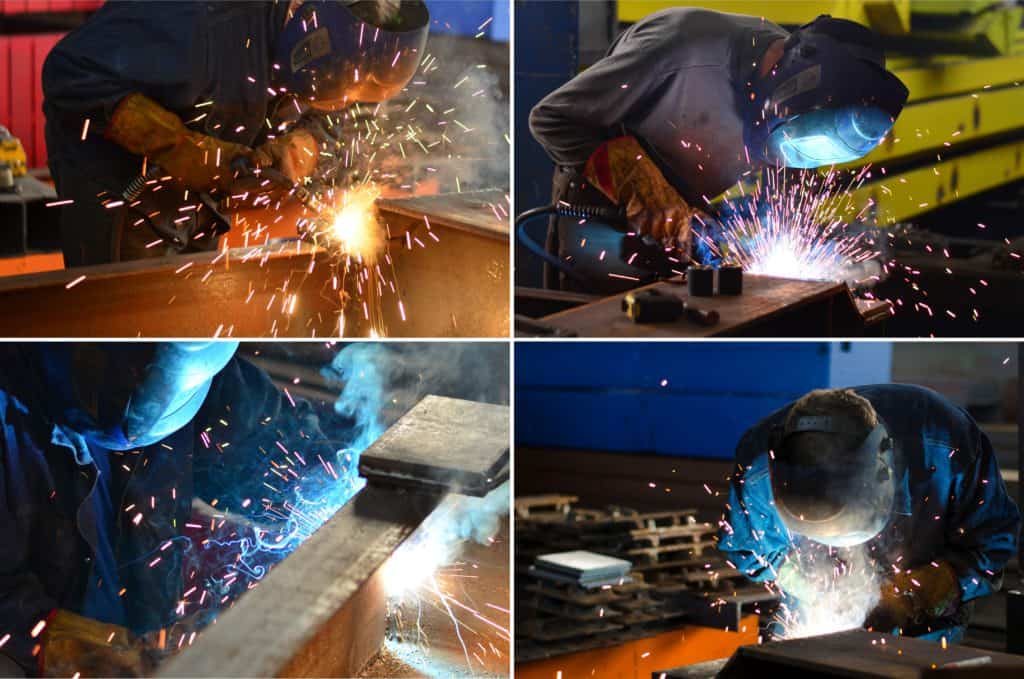
Surface Finishing
To maintain the metal’s visual appeal, enhance its lifespan, and protect it from corrosion, surface finishing and coating are critical stages of sheet metal fabrication. Here is a list of some popular techniques used for these processes:
- Grinding and sanding: Finishing touches, such as grinding and sanding, are necessary to create a polished look on sheet metal by wiping away blemishes or rough patches. The result is an even surface that appears flawless.
- Polishing: Applying polishing processes can create a lustrous finish on the sheet metal’s surface, elevating its shimmer and reflective qualities.
- Powder coating: Transform your sheet metal with the power of powder coating. Applying a dry, protective layer to the surface and curing it in an oven can create a resilient coat that will hold up against chipping, scratching, and fading over time. With this protection method at your disposal, nothing stops you from getting maximum durability from your investments!
- Paint: Painting helps protect sheet metal against corrosion, enhancing its overall appearance and creating a solid, lasting protective layer.
- Anodizing: For maximum longevity and protection from corrosion, anodizing is the best way to finish sheet metal. This process involves submerging it in a conducting fluid and passing electricity through the material to produce a protective oxide layer that defends against rust or wear and tear.
- Plating: Nickel or chrome is applied to sheet metal surfaces to improve their aesthetic appeal and protect them from wear.
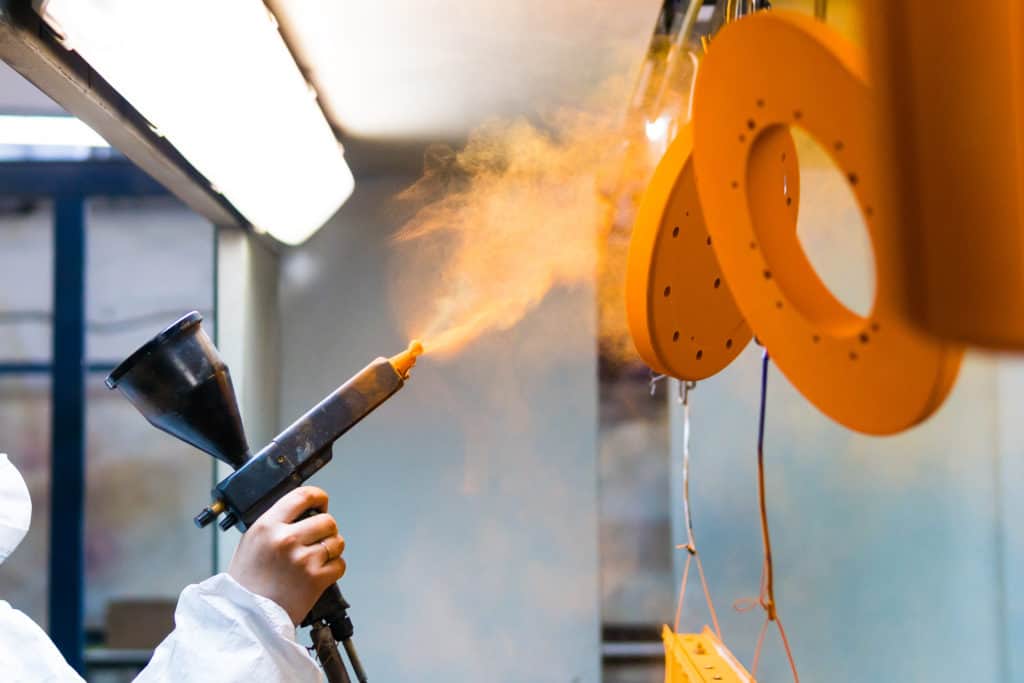
Inspection and Quality Control
Ensuring quality assurance of final sheet metal products is a crucial step in the fabrication process. It guarantees that your ultimate product fulfills the required standards and serves its designated purpose. To ensure the high quality of finished parts, here are a few tips for inspecting:
- Control procedures: Develop explicit quality control systems and specifications, such as assessment checklists and approval criteria, to ensure all completed items comply with the essential quality guidelines.
- Inspect for defects: Thoroughly examine finished products to ensure they are free of any scratches, dents, or other flaws that could decrease the product’s quality, reliability, and performance.
- Check dimensions: Compare completed product measurements to the technical specifications to guarantee accuracy and compliance with required tolerances.
- Test functionality: Thoroughly test the finished products to ensure they function correctly and meet all performance requirements.
- Document results: Record the outcomes of your quality assurance and inspection process, noting any flaws or problems discovered and corrective measures taken.
- Continuous improvement: Utilize the inspection and quality control process results to spot potential areas for improvement, then make necessary changes to boost the overall standard of completed products.
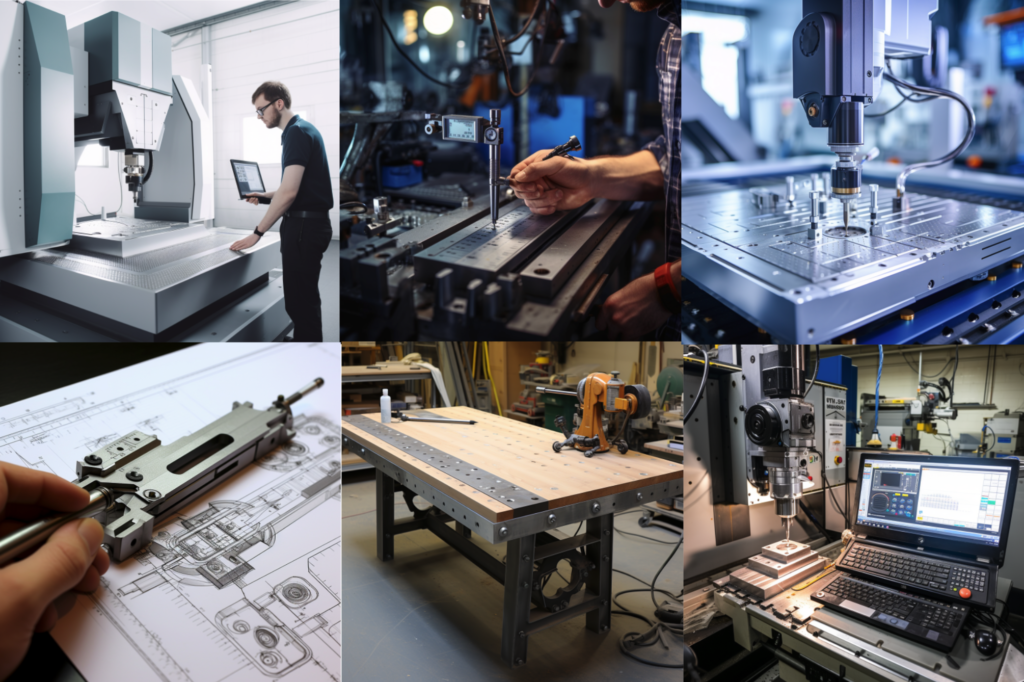
Maintenance Equipment and Tools
Consistent upkeep and maintenance are critical to the longevity of sheet metal equipment and tools. Not only will proper care help prolong their lifespan, but it can also save you time and money on costly repairs or downtime. Here are a few tips for preserving your sheet metal apparatus:
- Regular cleaning: Maintaining sheet metal equipment and tools is paramount to ensure their superior performance, so routinely clean them with a soft cloth and mild cleaner to rid any dirt, dust, or debris. Doing this will guarantee the optimal functionality of your machines.
- Lubrication: Maximize the performance of your sheet metal equipment and tools by lubricating moving parts, such as bearings, gears, and slides. It will ensure a seamless operation while avoiding excessive wear on mechanical components.
- Inspection: Periodically examine all sheet metal gear and tools for any signs of tear and wear, including fractures in blades, worn bearings, or screws that are not tight. Replace the damaged elements when necessary to ensure optimal performance.
- Calibration: Consistently evaluate sheet metal equipment and tools to guarantee that they function within the required tolerances and specifications for optimal performance.
- Storage: To preserve the life of your sheet metal equipment and tools, always store them in a cool and dry environment. Furthermore, protective covers must be used over each machine or device to avoid dust and debris accumulation.
- Proper use: Always follow the manufacturer’s directions and abide by safety protocols when using sheet metal equipment and tools. Doing so will ensure their optimal performance, effectiveness, longevity, and safety. Avoid attempting activities not designed for the machines, which may harm or decrease their lifespan.
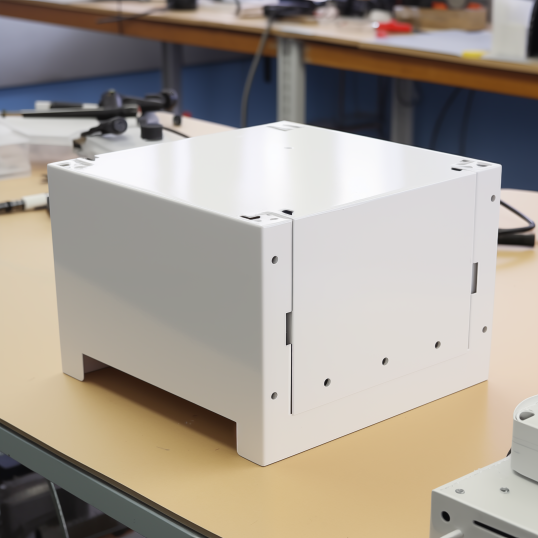
Conclusion
Stating sheet metal mandates meticulous attention to detail and maintaining quality standards throughout the process. By being mindful of the characteristics and properties of sheet metal, selecting suitable materials and tools accordingly, and adhering to exact measuring processes when cutting, shaping, or connecting components – you can guarantee that finished products abide by strict quality regulations while fulfilling their desired purpose.
Furthermore, monitoring equipment maintenance will help avoid costly repairs and downtime.By adhering to these standards, your sheet metal fabrication projects will be guaranteed success. Indeed, creating with sheet metal necessitates close attention to detail and absolute commitment to the highest quality throughout every process step.
FAQS
To ensure accuracy when cutting sheet metal, it is essential to use a saw or shear designed explicitly for the material. Additionally, take your time and measure twice. Finally, be sure to account for any warping or distortion in the fabric before cutting so that you can adjust accordingly.
To ensure that your bends are precise, use a jig to keep the part secure while bending. It is also vital to check features between each bend as some materials may have slight changes in angle when bent. Use a die explicitly designed for the material and thickness you are working with. Finally, take your time to make sure each bend is in the right place before moving on to the next one.
When painting sheet metal projects, it is vital to start by scrubbing away any dirt or debris from the surface and then allowing it to dry completely before painting. It would be best to use a primer to help prevent corrosion and ensure even paint coverage. Once you have finished priming and painting, allow ample time for drying between each coat and an overall drying period before using or handling the piece.
Common surface defects can include scratches, dents, pinholes, tears, or creases in the material and warping due to heat treatment. Scrutinizing your sheet metal before beginning any project and replacing any damaged material if necessary.
Working with sharp edges can be dangerous, so taking safety precautions while handling sheet metal is essential. Wear safety gear such as gloves and protective eyewear when operating power tools or cutting and bending metals. Also, ensure no loose clothing or jewelry could get caught in the machinery. Finally, take extra care when handling sharp edges and use a clamp or vise to help keep the material in place.
To prevent corrosion or rust, use a protective coating such as paint, powder, galvanizing, or anodizing. Additionally, store your metal in dry conditions and clean off any dirt or debris before applying the coating. If you’re working with metals subject to outdoor elements, consider using a sealant and/or wax to help keep out moisture. Finally, inspect the material regularly for signs of wear and tear to address any problems quickly.