Table of Contents
Understanding Laser Cutting
What is laser cutting?
A laser beam cuts and engraves various materials using concentrated laser beam. This modern technology melts, burns, or vaporizes the material to achieve precise results. This powerful, non-contact cutting method offers numerous benefits over traditional cutting techniques, making it a popular choice in various manufacturing operations.
Different types of lasers
When it comes to cutting metal, there are primarily two types of lasers to choose from:
- Fiber lasers: These generate a high-power laser beam using a fiber optic cable, making them suitable for cutting metals, including stainless steel, aluminum, and brass. Fiber lasers are known for their efficiency, speed, and low maintenance requirements.
- CO2 lasers: CO2 lasers produce a laser beam by exciting a gas mixture, primarily consisting of carbon dioxide. While they are versatile and can cut various materials, their effectiveness in cutting metal is generally lower than that of fiber lasers.
- Cryogenic lasers are also an option for sheet metal cutting. These use a combination of liquified gases such as nitrogen, helium, and hydrogen to create a freezing temperature focusing on the material that needs cutting. This type of laser is most commonly used for delicate and intricate cuts, as its cold beam doesn’t cause thermal stress on the material.
Laser Cutting Capabilities
Laser-cutting machines can handle various materials, including sheet metal, steel, and aluminum. The power required for cutting different materials depends on the material’s thickness and the type of laser used. Generally, a higher-power laser is needed to cut through thicker materials.
- Cutting sheet metal: Laser cutters can effectively cut sheet metal. Fiber lasers, particularly, are well-suited for this task, offering high precision and clean edges.
- Cutting sheet steel: Laser cutters can also cut sheet steel, with fiber lasers providing the best results.
- Cutting aluminum: While aluminum can be more challenging due to its high reflectivity and thermal conductivity, fiber lasers can successfully cut aluminum with appropriate adjustments to the laser’s parameters.
The thickness limitations
The thickness limitations for laser cutting depend on the laser’s power and the cut material.
A 1kW fiber laser can cut mild steel up to a thickness of 10mm, whereas a 6kW fiber laser can cut up to 25mm. The maximum thickness for cutting aluminum and stainless steel will be lower than for mild steel, as these materials require more cutting energy.
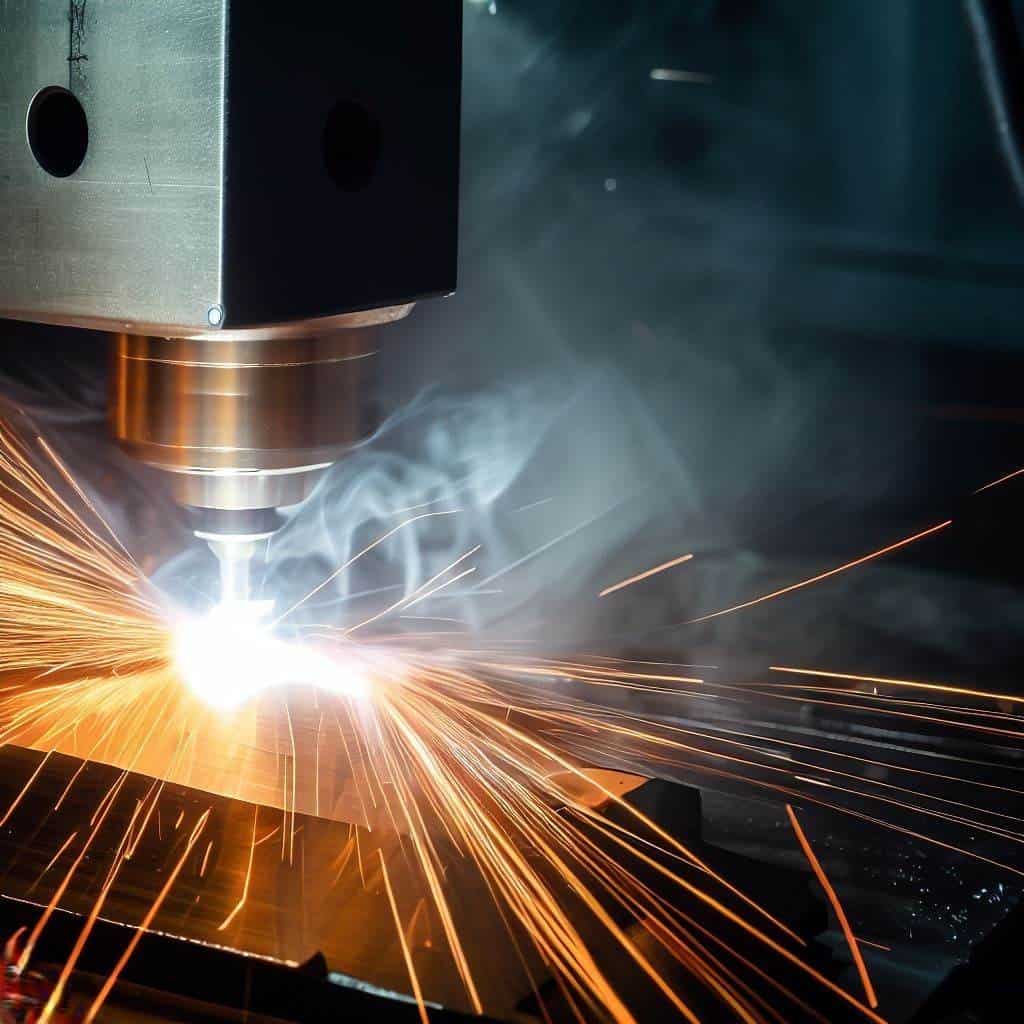
Laser Cutting Process
How laser cutting works
The laser cutting process involves three main components: the focused laser beam, molten material, and computer numerical control (CNC) system.
1. Focused laser beam: The laser cutting machine generates the laser beam and focuses onto the material’s surface using a series of mirrors and lenses. This focused beam has exceptionally high energy density, allowing it to melt, burn, or vaporize the material with exceptional precision.
2. Molten material and cutting process: As the focused laser beam moves across the material, it creates a narrow kerf (cut), with the molten material being ejected from the cut by an assist gas, such as nitrogen or oxygen. This process ensures clean and precise cuts with minimal heat-affected zones.
3. Computer numerical control (CNC): The movement of the laser cutting head and the material follows a CNC system, which interprets a digital design file and translates it into precise cutting paths. The procedure allows intricate designs and patterns to be cut accurately and repeatedly.
Comparing laser cutting to other cutting methods
- 1. Flame cutting: Also known as oxy-fuel cutting, flame cutting uses oxygen and fuel gas to cut through metal. While it can cut through thick metals at a lower cost, it lacks the precision, speed, and versatility of laser cutting. Flame cutting also produces larger heat-affected zones and may require additional finishing processes to clean up the cut edges.
- 2. Plasma cutting: To cut through metal, plasma cutting employs an electrically conductive gas, such as air or argon, to generate a high-temperature plasma arc. While plasma cutting can be faster than laser cutting for thicker materials, it generally produces less precise cuts with rougher edges. Additionally, plasma cutting is limited to conductive materials, whereas laser cutting can process a more comprehensive range of materials.
- 3. CNC machining: CNC machining is a subtractive manufacturing process that uses rotating cutting tools to remove material and create the desired shape. Although CNC machining can produce precise and well-finished parts, it can also lead to tool wear and tear due to the contact between the cutting tool and the machined material. Laser cutting, conversely, is a non-contact process that eliminates tool wear and can process a wider variety of materials.
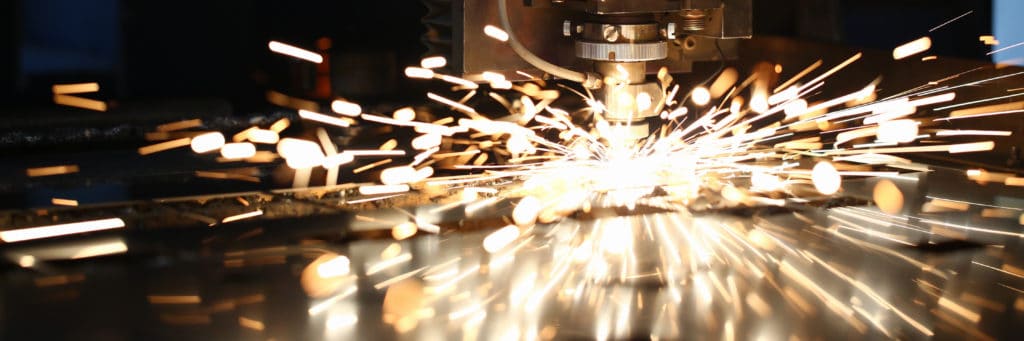
Pros and cons
Pros of laser cutting
- 1. High precision and quality: Laser cutting produces extremely precise cuts with smooth edges and minimal kerf width, one of its most significant advantages. This results in high-quality parts and components requiring minimal post-processing, saving time and resources.
- 2. Energy efficiency: The laser cutting process is efficient in terms of energy usage because the energy from the laser beam is concentrated on a small area, resulting in less waste of energy. Additionally, the latest laser-cutting machines are designed to enhance energy consumption, making them a more economical option over time.
- 3. Non-contact cutting process: Since laser cutting does not involve any physical contact between the cutting tool and the material, there is no tool wear or risk of material deformation due to pressure. By using this method, not only can the cutting equipment last longer, but delicate materials also can be cut without damage.
- 4. Versatility in materials and applications: Laser cutting can process various materials, including metals, plastics, wood, and more. The diversity of its uses makes it appropriate for many industries and purposes, including aerospace, automotive, electronics, and the manufacturing of medical devices.
Cons of laser cutting
- 1. High initial investment: Laser cutting machines can be expensive, particularly for high-power fiber lasers capable of cutting thick metals. Although the benefits may be greater in the long run than the initial costs, some businesses may need help to invest upfront.
- 2. Limitations in cutting certain materials: Although laser cutting is versatile, it may only suit some materials. For example, materials with high reflectivity, such as copper and brass, can pose challenges due to the risk of back-reflection damaging the laser source. Moreover, there may be more optimal approaches for cutting exceptionally thick materials.
- 3. Potential safety risks: The high-intensity laser beam used in laser cutting can pose safety hazards if not handled properly. It is necessary to have safety measures, such as protective eyewear, safety interlocks, and enclosed cutting chambers, to minimize the risk of injury or damage to equipment.
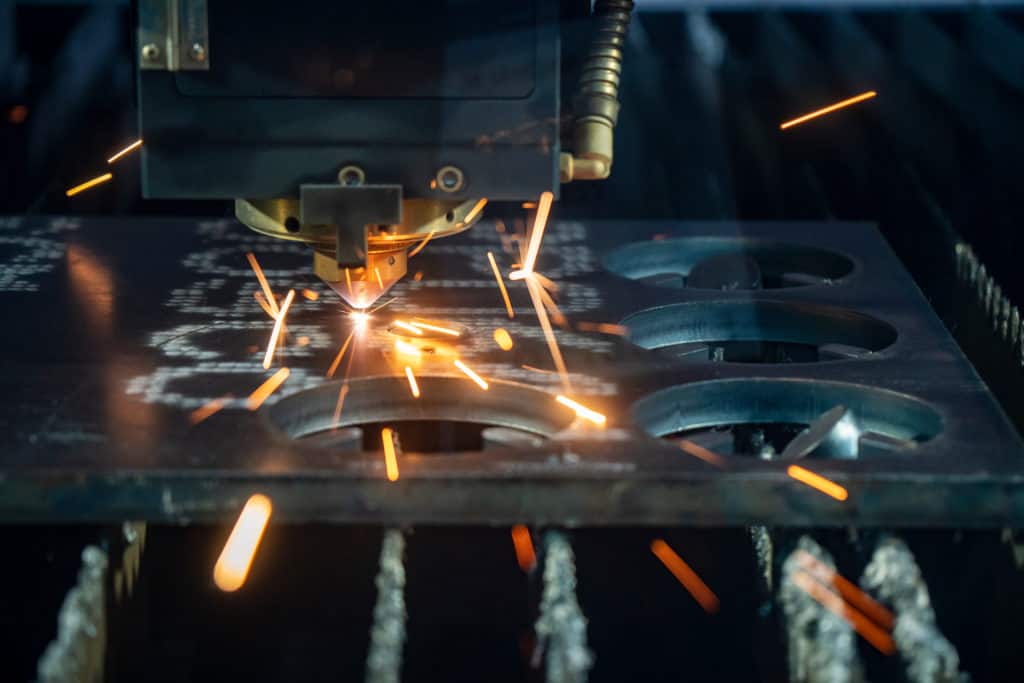
Laser Cutting Applications
Aerospace industries
Laser cutting is crucial in the aerospace industry, where precision and accuracy are paramount. The process cuts and shapes various components, such as turbine blades, engine parts, and structural components. Laser-cut parts’ high precision and quality ensure optimal performance and safety in aerospace applications.
Manufacturing companies
- 1. Sheet metal fabrication: In sheet metal fabrication, laser cutting is invaluable for creating intricate designs and shapes with high precision. Manufacturers can use it to make various items such as enclosures, brackets, and panels while minimizing waste and efficiently utilizing materials.
- 2. Injection molding: Laser cutting is often used in the injection molding industry to create molds and dies with exceptional accuracy and surface finish. The process allows for producing complex geometries and fine details that may be challenging to achieve through conventional machining methods.
Automotive and other manufacturing operations
In the automotive industry, laser cutting creates various components, such as body panels, chassis, and interior components. The process ensures high-quality parts with tight tolerances, contributing to improved vehicle performance, safety, and aesthetics.
Moreover, laser cutting has extensive applications in diverse manufacturing operations involving electronics, medical device production, and the fashion industry. The technology’s ability to operate with precision, versatility, and process various materials makes it an invaluable tool for multiple applications.
Safety and Environmental Concerns
Risks and side effects of laser technology
While laser cutting offers numerous benefits, the technology has some risks and side effects. These include:
- 1. Eye hazards: The high-intensity laser beam can cause severe eye damage if proper safety measures are not in place. Protective eyewear, safety interlocks, and enclosed cutting chambers can minimize injury risks.
- 2. Burns and fire hazards: The laser cutting process generates heat, which can cause burns or even start fires if not properly managed. An adequately ventilated fire suppression system is essential for a safe work environment.
- 3. Fumes and particulates: Laser cutting can produce harmful fumes and particulates, particularly when cutting certain materials like plastics. Installing suitable ventilation and filtration systems is vital to minimize exposure to toxic byproducts.
Disadvantages of medical lasers
Medical lasers have revolutionized various treatments and procedures; however, they also have some disadvantages, including:
- 1. Cost: Medical lasers can be expensive regarding initial investment and ongoing maintenance costs.
- 2. Training requirements: Medical professionals need specialized training to operate and maintain laser equipment safely and effectively.
- 3. Tissue damage: If not used correctly, medical lasers can cause unintended tissue damage, leading to complications and longer patient recovery times.
Environmental impact
Laser cutting can have negative environmental impacts, such as producing harmful gases and waste.
1. Harmful gases: Laser cutting can produce harmful gases like dioxins and volatile organic compounds (VOCs) when cutting certain materials, particularly plastics. Having adequate ventilation and filtration systems is crucial for reducing the emission of these gases into the environment.
2. Waste production: The laser cutting process generates waste from scrap material and used consumables, such as lenses and filters. Implementing waste reduction strategies like recycling and reusing materials whenever possible is crucial for reducing the environmental impact.
By addressing these safety and environmental concerns, businesses can ensure that their laser-cutting operations remain sustainable and responsible while enjoying the technology’s many benefits.
Conclusion
This article explored the various aspects of sheet metal laser cutting, including understanding the technology, the process, advantages and disadvantages, applications across different industries, and safety and environmental concerns. We have seen that laser cutting offers high precision, quality, and versatility, making it an essential tool for numerous industries and applications.
However, laser technology has challenges and risks, such as high initial investment, limitations in cutting certain materials, and potential safety hazards. Businesses can make the most of laser-cutting technology by addressing these concerns and implementing proper safety measures while minimizing potential drawbacks.
As the demand for precision and efficiency grows in various industries, laser-cutting technology will undoubtedly play an increasingly vital role. We encourage you to delve deeper into sheet metal laser cutting and explore this cutting-edge technology’s many opportunities. A laser-cutting business can be a profitable and rewarding venture with the right approach, investment, and commitment to quality and safety.
FAQS
Material thickness plays a significant role in laser cutting. Thicker materials may require more powerful lasers or slower cutting speeds to achieve the desired results. The maximum thickness possible will depend on the specific laser cutter and its capabilities. Most manufacturing industries utilize laser cutting machines that can handle various material thicknesses to meet their production needs.
Yes, laser cutting is suitable for cutting mild steel, as well as other metals such as stainless steel, aluminum, and more. Different cutting operations may require adjustments to the laser’s settings and power, but laser cutters are versatile and can handle various metal materials in various industries.
Metal thickness affects the laser cutting process regarding the required laser power, cutting speed, and overall cut quality. Thicker materials may necessitate more powerful lasers or slower cutting speeds. The optimal cutting parameters will depend on the specific laser-cutting machine’s capabilities.
Laser cutting works with metals, plastics, wood, and other materials. It is a versatile technique. The laser cutting process can be adjusted to accommodate different materials, ensuring precise and clean cuts across an extensive array of applications in industrial manufacturing.
The fusion cutting process utilizes a laser beam to heat a material until it reaches melting. A high-pressure gas, such as nitrogen or argon, is then used to blow away the molten material, creating a clean and precise cut. Fusion cutting uses for cutting metals like stainless steel and aluminum.
Yes, laser cutters can produce intricate sheet metal parts due to their high precision and ability to cut complex shapes. They can work with metal sheets of varying thicknesses and materials, creating versatile production capabilities for various industries.
Laser cutting has several advantages over other cutting processes, such as plasma or mechanical. Cutting complex shapes and intricate designs is made possible by higher precision, reduced material waste, and better edge quality. Laser cutting is also more energy-efficient and can work with many materials, including metals, plastics, and wood.
The upfront costs of laser cutting equipment can be high, particularly for high-power machines capable of cutting thick materials. However, the long-term benefits of precision, reduced waste, and versatility often outweigh these initial costs. Many manufacturing industries invest in quality laser-cutting services to streamline production processes and improve efficiency.
Seed lasers generate the initial laser beam, amplified to achieve high power through various techniques, such as fiber amplification or other gain media. High-power lasers are crucial for cutting thick materials and achieving faster cutting speeds, making them essential components in most manufacturing companies’ laser cutting systems.
A laser cutter can cut sheet metal with high precision and accuracy. Laser cutting is often considered superior to other cutting processes due to its non-contact nature, which results in less material distortion and a cleaner edge. Additionally, laser cutting services can handle a wide range of metal thicknesses and offer greater flexibility in design and complexity.
Laser cutting offers several advantages over other cutting methods, such as plasma and mechanical. Cutting complex shapes and designs is more accessible with higher precision, less material waste, and better edge quality. Laser cutting is also a non-contact process, which helps prevent material distortion.