Exploring metal coatings can unlock numerous benefits for materials across various industries, enhancing durability, resistance, and aesthetic appeal. With our expertise, we’re here to guide you through the intricate details and applications of metal coatings, ensuring you find the perfect solution for your needs.
Metal coatings, essential for protecting surfaces against corrosion, enhancing appearance, and improving properties, include galvanizing, anodizing, powder coating, electroplating, and thermal spraying. Each type serves unique functions, from corrosion resistance to aesthetic enhancement, catering to industrial and decorative needs.
Delve deeper into the fascinating realm of metal coatings with us. From understanding the science behind each type to discovering their practical applications and maintenance tips, we have a wealth of information waiting for you.
Table of Contents
Metal Coatings Across Industries
Metal coatings are critical in enhancing the longevity and functionality of metal components used in various sectors. These coatings safeguard metals from corrosion, wear, and environmental impacts by applying a protective layer, ensuring their durability and performance.
This post aims to demystify the world of metal coatings, shedding light on the metal coating process, types of metal coatings like powder coatings and paint coatings, and their benefits. We will also address commonly asked questions to thoroughly understand how metal coatings offer excellent corrosion resistance and contribute to the improved quality of metal products.
Defining Metal Coatings
Metal coatings refer to a protective barrier applied to the outer surface of metallic objects to prevent metal corrosion and damage. This coating process involves depositing a thin layer of material—such as paint, powder, or a metallic finish—onto the metal substrate, enhancing the metal’s surface with qualities like wear resistance and electrical conductivity.
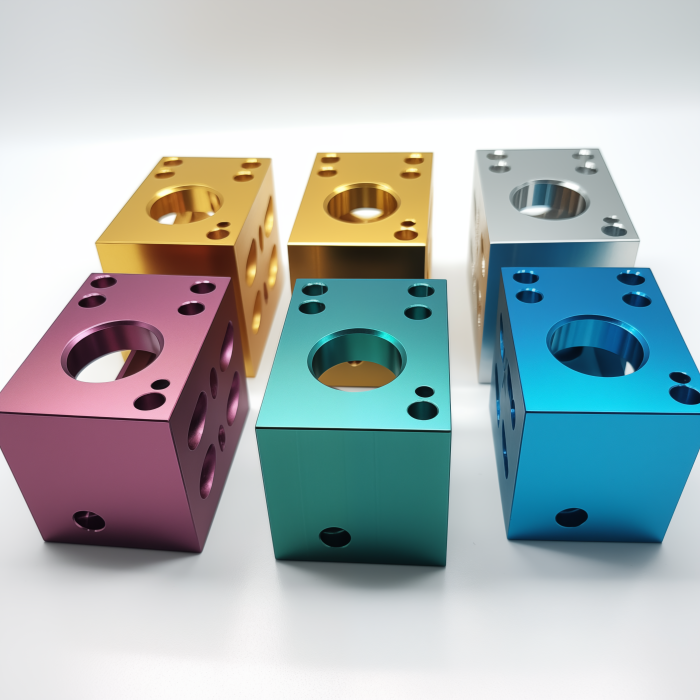
Diverse Types of Metal Coatings
Metal coatings can be broadly categorized into several types, each with its unique coating technique and purpose:
- Galvanizing: This method, particularly hot dip galvanizing, involves immersing metal in molten zinc to form a zinc coating that offers high corrosion resistance. The zinc layer acts as a sacrificial barrier, protecting the steel substrate from oxygen and carbon dioxide.
- Anodizing: An electrochemical process that converts the metal surface into a durable, corrosion-resistant, anodized finish. Commonly applied to aluminum, it enhances the formation of aluminum oxide, providing a protective coating that can resist harsh environmental conditions.
- Powder Coating: A dry coating process where powdered particles are applied electrostatically to the metal surface and then cured under heat. This electrostatic process results in a uniform, durable, and aesthetically versatile protective layer without using volatile organic compounds (VOCs).
- Electroplating: This involves depositing metal ions onto the metallic surface through an electrolytic solution using an electric current. The electroplating process can apply thin coating layers of precious metals for improved appearance, corrosion resistance, and electrical conductivity.
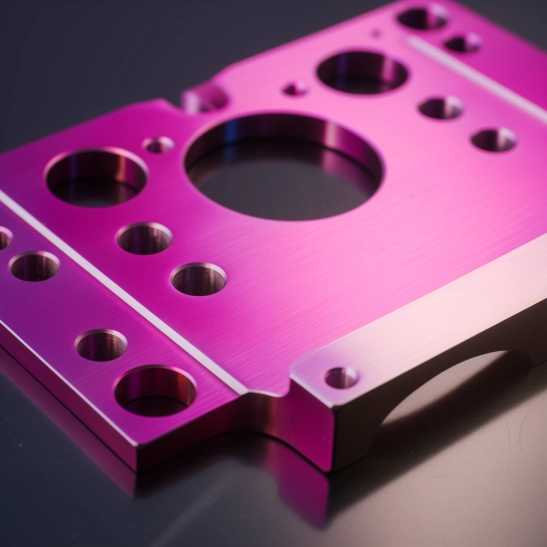
These methods ensure that all the applied coatings, from paint coatings to more specialized aluminum and titanium coatings, provide a thin yet robust protective layer. The coating thickness and type are chosen based on the metal component’s intended use, offering everything from excellent corrosion protection to enhanced functional properties on an industrial scale.
Types of Metal Coatings
In the intricate world of metal coatings, understanding the various types and their applications is crucial for enhancing metal components’ durability, functionality, and aesthetic appeal. Galvanizing, anodizing, powder coating, and plating are key techniques employed in the metal coating process, each offering unique advantages to protect and beautify metallic surfaces.
Galvanizing
Galvanizing, a method where steel or iron is coated with molten zinc through hot dip galvanizing, is celebrated for its galvanic protection against corrosion. This process not only covers the coated object with a layer of zinc coatings but also ensures superior protection against oxygen and carbon dioxide, crucial elements in the corrosion process. The galvanizing process typically achieves a coating thickness of 45 to 85 micrometers, resulting in galvanized surfaces known for their durability and excellent corrosion resistance.
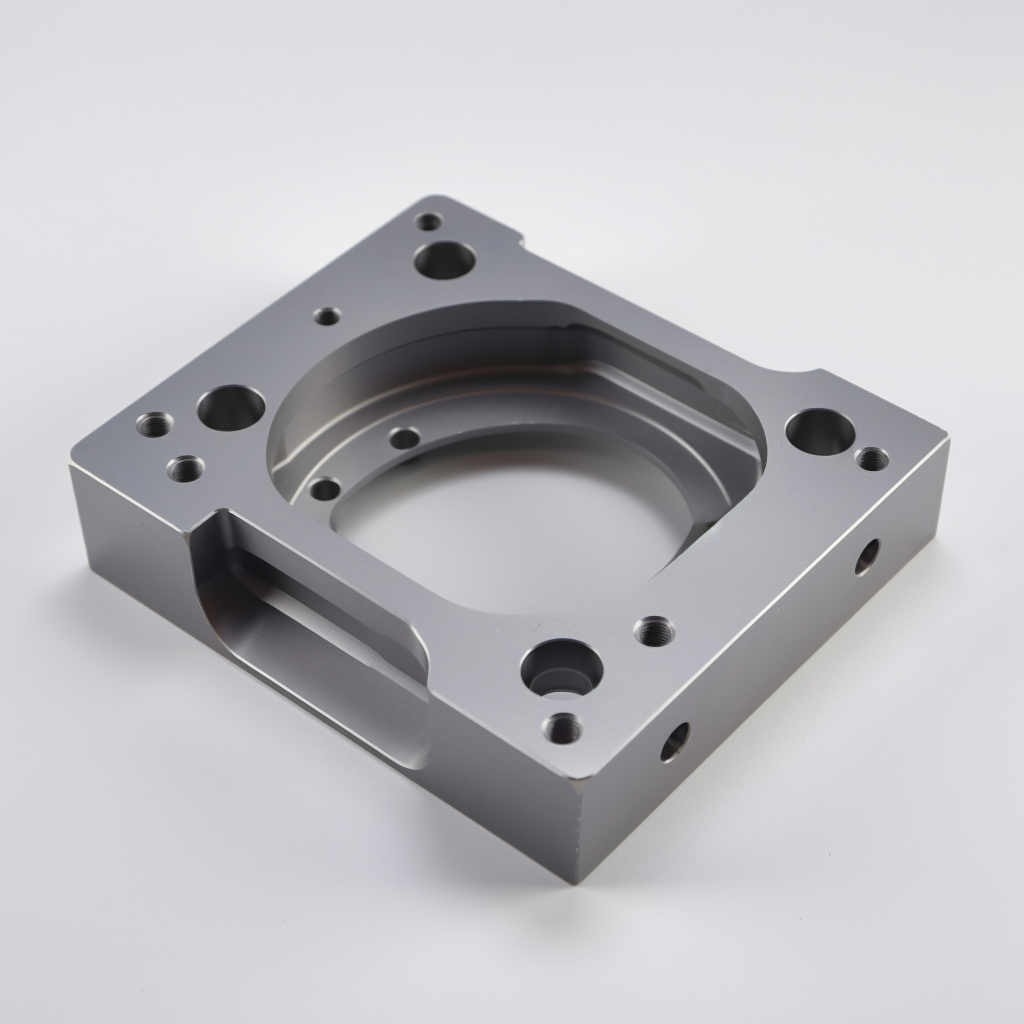
Anodizing
Anodizing differs significantly from galvanizing by enhancing the natural oxide layer on metals such as aluminum through an electrochemical process. This coating technique involves an electrolytic solution where an electric current is used to form aluminum oxide, a protective layer that can be dyed in a variety of colors for aesthetic purposes. Anodized finishes, ranging from vibrant reds to deep blacks, offer not only enhanced wear resistance but also protection against the effects of carbon dioxide and other corrosive elements, with a typical coating thickness of 5 to 25 micrometers.
Powder coating
Powder coating stands out as a modern coating process that applies dry powder onto metallic surfaces using spraying equipment before curing it into a solid layer. This method offers a significant advantage over traditional paint coatings by eliminating volatile organic compounds (VOCs) and providing various colors and finishes.
Powder coatings, applied through an electrostatic process and cured under heat, produce a uniform and durable layer ranging from 25 to 300 micrometers in thickness. This type of coating is ideal for various applications, including outdoor furniture and automotive parts, offering excellent corrosion resistance and aesthetic flexibility.
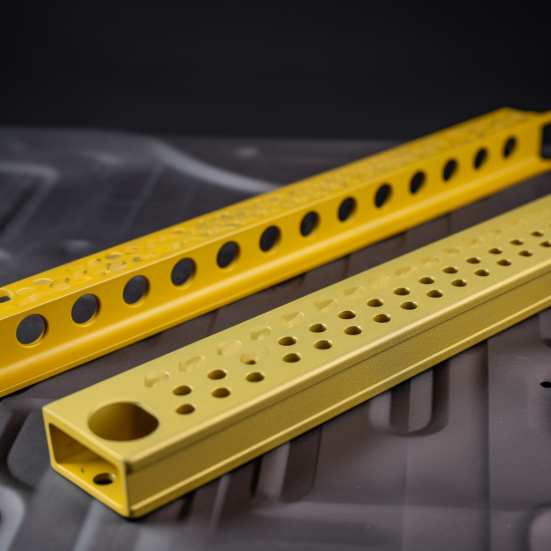
Plating
Plating, encompassing techniques like electroplating and electroless plating, deposits a thin layer of metal ions onto a substrate through an electrical current or chemical reaction, respectively. This metal coating process, including ion plating and thermal spraying, can apply metals like chrome, nickel, or gold onto metallic objects, providing a lustrous finish and additional corrosion resistance. The coating thickness for plating is meticulously controlled, typically between 0.5 to 20 micrometers, catering to a wide array of industrial and decorative needs.
Characteristics | Galvanizing | Anodizing | Powder Coating | Plating |
Materials Used | Zinc on steel or iron | Aluminum oxide on aluminum | Polymer resins, pigments, and curatives | Metals (chrome, nickel, gold, etc.) on various substrates |
Coating Thickness (micrometers) | 45 – 85 | 5 – 25 | 25 – 300 | 0.5 – 20 |
Color Options | Silver (limited) | Wide range (blacks, blues, reds, etc.) | Very wide range of colors and finishes | Depends on the metal used (gold, silver, etc.) |
Corrosion-Resistance Strength | High | Moderate to high | High | Variable, based on metal used |
Cost | Low | Moderate | Moderate to high | High |
These metal coatings, from zinc coatings in galvanizing to aluminum coatings in anodizing and the diverse colors available through powder coating, play a pivotal role in protecting metal components from corrosion, wear, and environmental damage. The choice of coating material, method, and thickness is tailored to the specific requirements of the metal substrate, whether it’s steel, aluminum, or copper, ensuring the metal components’ longevity and performance.
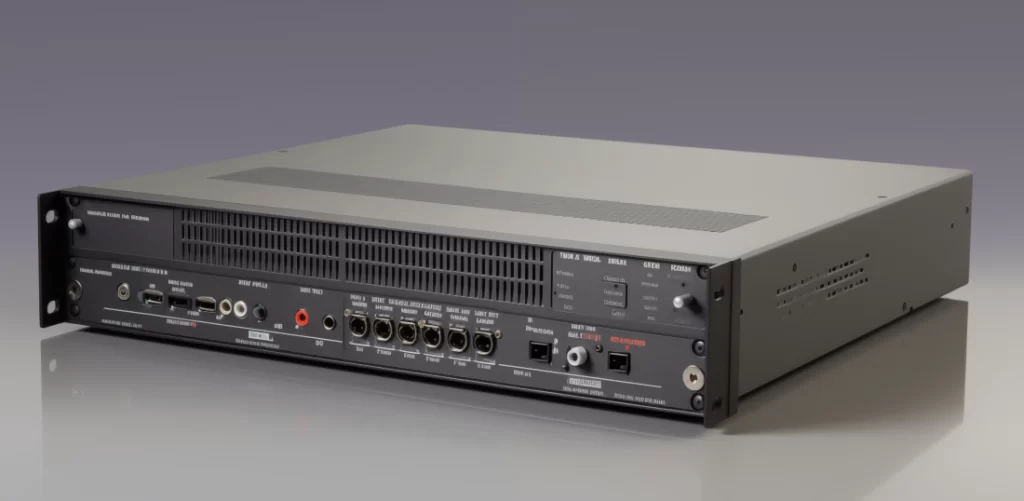
Factors to Consider When Selecting a Metal Coating
Selecting the right metal coating for your project is a pivotal decision that impacts the durability, functionality, and aesthetic appeal of metal components. This section provides a comprehensive guide on the considerations for choosing a metal coating, compares different coatings for specific applications, and offers expert advice on tailoring coating types to industrial needs, incorporating key terms to enhance understanding and application.
Material Type: The base metal’s composition is vital in determining the appropriate coating. Aluminum is ideal for anodizing to create durable, anodized surfaces, while steel and iron are perfect candidates for zinc coatings through the galvanizing process, offering galvanic protection against corrosion.
Environmental Conditions: The operating environment dictates the need for coatings with superior corrosion resistance. Galvanized steel, with its zinc coatings, and powder coatings are excellent choices for combating the corrosive effects of humidity and saltwater.
Budget: The cost is a significant factor; galvanizing offers a cost-effective solution, while powder coatings and the electroplating process might represent higher initial investments but provide value in terms of longevity and aesthetic versatility.
Aesthetic Requirements: Desired visual outcomes influence the selection. Powder coatings offer a wide spectrum of colors and finishes, from matte to glossy, while electroplating can impart a luxurious sheen to metallic objects.
Wear and Impact Resistance: For high-traffic or mechanically stressed components, coatings like powder coatings, known for their thickness and durability, ensure the metal component remains protected and visually appealing.
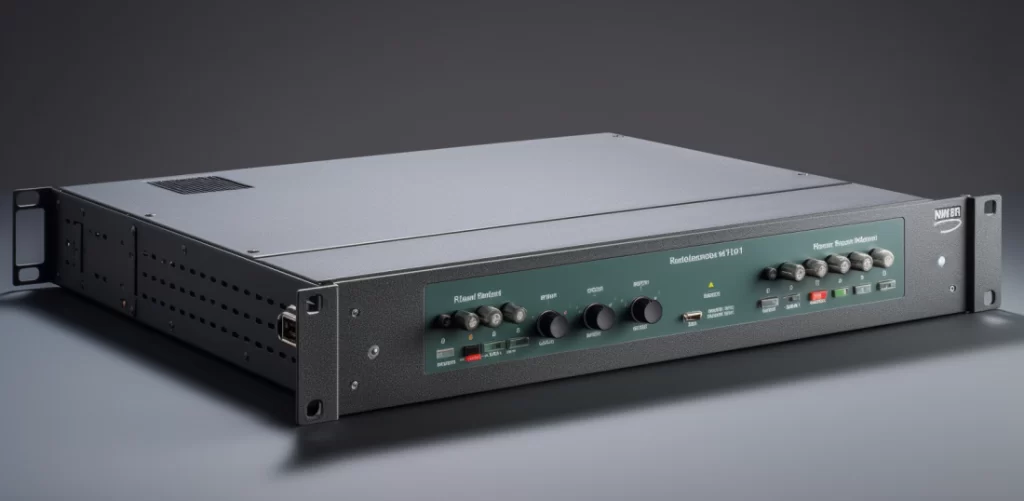
Comparison of Different Coatings for Specific Applications
Outdoor Structures: The galvanizing process is preferred for outdoor applications, thanks to its cost-efficiency and corrosion resistance, making it suitable for structures exposed to the elements.
Aerospace and Automotive Components: Anodizing provides lightweight, corrosion-resistant metal substrates for aluminum parts, essential in weight-sensitive applications like aerospace and automotive industries.
Consumer Goods: Consumer electronics and appliances benefit from powder coatings, which offer a durable and attractive finish, essential for the longevity and appeal of electronic devices.
Decorative Finishes: The electroplating process is chosen for decorative applications, providing coated metal with a high-end finish, ideal for jewelry and automotive trims.
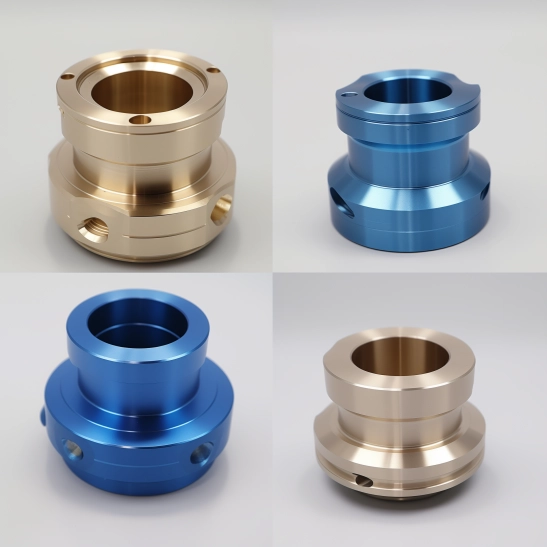
Advice on Matching Coating Types with Industrial Needs
Consulting with specialists in metal coatings can provide insights into selecting the right type of metal coatings, whether it’s paint coatings, ceramic coatings, or other metal coatings. Proper surface preparation is crucial to ensuring that the coating adheres well to the metal’s surface, with techniques varying from simple cleaning with mild detergents to more complex processes involving electrical currents and spray guns.
It’s also important to consider the natural process by which metals react with their environment and how different coatings can mitigate these reactions. For instance, coatings provide a barrier preventing oxygen and moisture from initiating corrosion. Understanding the specific reactions of metals like iron forming iron oxide (rust) can guide the selection of coatings that offer the best protection.
What is the strongest coating for metal?
The toughest paints for metal surfaces are recognized as epoxy paint and polyurethane paint. These coatings are highly favored for their exceptional durability and resistance to chemicals, abrasion, and impact, making them ideal for protecting metal in severe conditions.
Epoxy paint for metal is renowned for its robust adhesive properties, forming a hard, protective layer that shields metal surfaces from corrosion, chemicals, and harsh environmental conditions. It is particularly effective in industrial settings and areas with high humidity or chemical exposure.
Polyurethane paint for metal offers a durable finish resistant to UV light, weathering, and many chemicals. It provides a flexible coating that can withstand expansion and contraction without cracking, making it suitable for outdoor applications where the coating needs to endure varying temperatures and conditions.
What is the most durable metal finish?
The most durable metal finish for corrosion resistance and longevity, especially in harsh environments, is galvanizing. This process coats steel or iron with zinc, creating a protective barrier extending the metal’s life. Galvanizing is ideal for industrial and outdoor applications due to its robust protection against rust and low maintenance needs. While powder coating offers aesthetic versatility and resistance to chemicals and abrasion, galvanizing stands out for its superior corrosion resistance.
Which coating is best for steel?
Considering overall protection, durability, and cost-effectiveness, three commonly recommended coatings are:
1. Galvanizing: Ideal for outdoor or corrosive environments, galvanizing involves coating steel with a layer of zinc, offering excellent corrosion resistance through galvanic protection.
2. Epoxy Coatings: Known for their superior adhesion and corrosion resistance, epoxy coatings are great for industrial applications, including pipelines and tanks, providing a tough, protective layer.
3. Powder Coatings: Offering a wide range of colors and finishes, powder coatings provide a durable, attractive finish that is resistant to chipping, scratching, and fading, suitable for indoor and outdoor applications.
Each of these coatings has its advantages and is best suited to different conditions and requirements. Galvanizing is often chosen for its long-lasting protection against corrosion, epoxy coatings for their strength and chemical resistance in industrial settings, and powder coatings for their aesthetic flexibility and overall durability.
Conclusion
Selecting the right metal coating is essential for protecting steel in various environments and applications. Galvanizing offers outstanding corrosion resistance for industrial and outdoor use, while powder coating provides a durable and aesthetically versatile finish. Choosing the appropriate coating ensures steel’s longevity, functionality, and appearance, highlighting the importance of matching the coating to the application’s specific needs.
Frequently Asked Questions
Powder coating is a dry finishing process where a powder material is electrostatically applied to a surface and then cured under heat, forming a hard, durable finish.
Yes, anodized aluminum can be dyed in a wide range of colors, offering both decorative and functional benefits.
Anodizing is an electrochemical process that converts the metal surface into a durable, corrosion-resistant, anodic oxide finish. This is typically used for aluminum, enhancing its natural oxide layer.
Metal plating involves depositing a thin layer of metal onto a substrate, enhancing the material’s corrosion resistance, electrical conductivity, and aesthetic appeal.
Galvanized coatings can last 50 years or more in most rural environments and 20 to 25 years in severe urban and coastal exposure.
Anodizing provides increased corrosion resistance, surface hardness, and improved aesthetic appeal through coloration, while also being environmentally friendly.
Powder coating offers superior durability, impact resistance, and environmental benefits by eliminating volatile organic compounds (VOCs) found in traditional liquid paints.
Electroplating uses electrical current to reduce dissolved metal cations to develop a coherent metal coating, while electroless plating relies on chemical reduction without external electrical power.
Yes, through a process called electroless plating, non-metal surfaces can be coated by first applying a special base layer that allows the metal to adhere.
No, powder coating comes in a vast array of colors and finishes, including glossy, matte, and textured options.