In CNC machining, achieving ultra-smooth finishes with Ra values of 0.4 μm or less can significantly impact your manufacturing costs. While high-quality finishes are essential for certain applications, understanding where you might be overspending can help optimize your production budget without compromising quality.
Ultra-smooth CNC finishes (Ra ≤0.4 μm) often lead to unnecessary costs when surface quality requirements exceed functional needs. The main factors driving these excess costs include over-specification of surface roughness, inefficient design choices, material selection issues, batch size decisions, and suboptimal machining strategies.
Let’s explore these cost factors in detail and discover practical strategies to optimize your CNC finishing costs while maintaining necessary quality standards.
Table of Contents
1. Over-Specification of Surface Roughness
Over-specification of surface roughness occurs when engineers or designers require smoother surface finishes than what’s functionally necessary for a part. This common pitfall in CNC machining happens when specifications demand extremely fine surface finishes (Ra ≤0.4 μm) for components that could function perfectly well with standard machined surfaces. It’s like paying for a mirror finish on the inside of an engine block – technically achievable, but unnecessarily expensive.
Unnecessary Polishing
When parts require mirror-like finishes (Ra 0.1-0.4 μm), manufacturers must add post-machining steps such as manual polishing or electropolishing to achieve these ultra-smooth surfaces. These additional processes significantly increase both production time and labor costs. For example, a standard machined surface might take 30 minutes to complete, but achieving a mirror finish could require an extra hour of manual polishing work, leading to that 15-20% cost increase in your overall manufacturing expenses.
Application Mismatch Examples
Application mismatches occur when high-quality finishes are specified for surfaces where they provide no functional benefit. For instance, specifying a 0.4 μm Ra finish for structural brackets that have no moving or visible surfaces can increase costs by 20% without adding any value.
Another example is requiring polished surfaces for internal components that never make contact with other parts or remain hidden from view. These mismatches often stem from applying the same surface finish requirements across an entire part rather than specifying different finishes for different surfaces based on their function
Surface Roughness vs. Cost Comparison
The relationship between surface finish quality and cost follows a clear pattern, as shown in the following comparison table:
Ra (μm) Finish Type Cost Impact Ideal Use Case
3.2 Rough milled Base price Non-visible internal parts
1.6 Standard machined +2.5% Functional mechanical surfaces
0.8 Fine machined +5% Sliding/rotating components
0.4 Polished +15% Optical/aesthetic surfaces
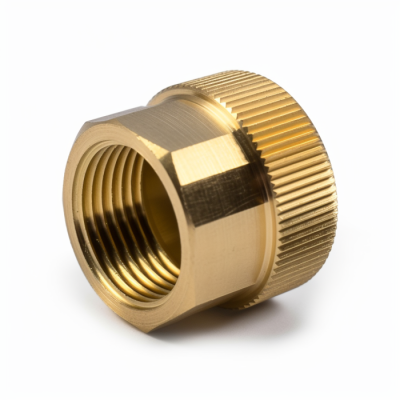
2. Inefficient Design Choices
Inefficient design choices in CNC machining refer to part designs that unnecessarily complicate the manufacturing process or require more sophisticated machining operations than needed. These design decisions often stem from overlooking manufacturing constraints during the design phase, leading to increased production costs without adding functional value to the final part.
Complex Geometries
Complex geometries involve intricate features that require multi-axis machining (e.g., 5-axis) for completion. While 5-axis machining is powerful and sometimes necessary, it significantly increases hourly machine rates from $40-75 to $75-150 compared to simpler 3-axis operations.
For example, specifying complex curved surfaces or deep pockets with variable wall thicknesses might require 5-axis machining, even when simpler geometries could achieve the same functional requirements. This complexity not only increases machine time but also requires more sophisticated programming and setup procedures.
Tight Tolerances
Specifying unnecessarily tight tolerances, such as ±0.001″ for non-critical dimensions, can dramatically impact manufacturing costs. These tight tolerances force machines to operate at slower speeds and require multiple finishing passes to achieve the specified accuracy.
For instance, while a standard tolerance of ±0.005″ might allow for efficient machining speeds, tightening this to ±0.001″ could require reducing cutting speeds by up to 50% and adding verification steps. This leads to a 25-50% increase in machining time and associated costs, often without providing any functional benefit to the part.
Impact on Machining Time
The combination of complex geometries and tight tolerances significantly affects overall machining time and efficiency. When a part requires both intricate features and precise dimensions, manufacturers must:
- Use more expensive cutting tools
- Reduce cutting speeds and feeds
- Perform more frequent tool changes
- Add inspection steps between operations
- Include additional setup time for complex fixturing
This compounding effect means that what could have been a simple 2-hour machining job might extend to 4-6 hours, resulting in substantially higher production costs
Design Feature Standard Approach Complex Approach Cost Impact
Axis Requirements 3-axis 5-axis +87-100%
Tolerance Level ±0.005″ ±0.001″ +25-50%
Setup Time Single setup Multiple setups +30-40%
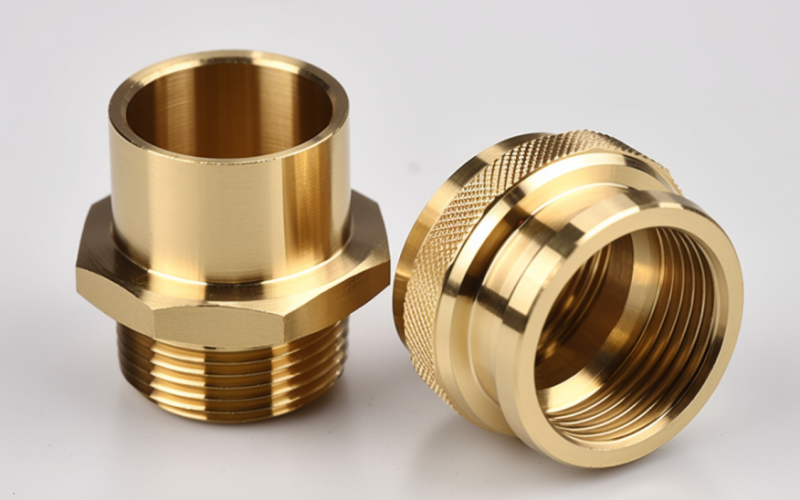
3. Material and Process Misalignment
Material and process misalignment occurs when there’s a mismatch between material selection, machining processes, and the desired surface finish requirements. This misalignment often results in inefficient manufacturing processes that drive up costs unnecessarily, especially when trying to achieve ultra-smooth finishes on challenging materials.
Hard-to-Machine Materials
Materials like stainless steel and titanium require significantly slower machining speeds compared to aluminum, directly impacting production time and costs. For example, while aluminum can be machined at 60 SFM (Surface Feet per Minute), titanium often requires reducing speeds to 30 SFM – a 50% reduction in cutting speed.
This speed reduction isn’t just about longer machining times; it also increases tool wear and requires more frequent tool changes. A part that might take 2 hours to machine in aluminum could require 3-4 hours in stainless steel while maintaining the same surface finish requirements.
Pre-finished vs. Standard Materials
Using standard materials that require extensive post-machining processes instead of pre-finished materials can lead to unnecessary costs. For example, starting with anodized aluminum that requires post-machining work creates additional steps and potential quality issues.
The anodized coating needs to be removed in areas requiring precise finishes, and the part may need re-anodizing after machining. This double-processing significantly increases both production time and cost compared to using standard materials and applying finishes only where needed.
Process Optimization Opportunities
Proper alignment of materials and processes can significantly reduce manufacturing costs while maintaining desired surface finishes.
Material Choice Common Misalignment Optimized Approach Cost Impact
Stainless Steel Standard speeds Optimized parameters -30%
Titanium Generic tooling Specialized inserts -25%
Pre-finished Post-process finishing Strategic material selection -20%
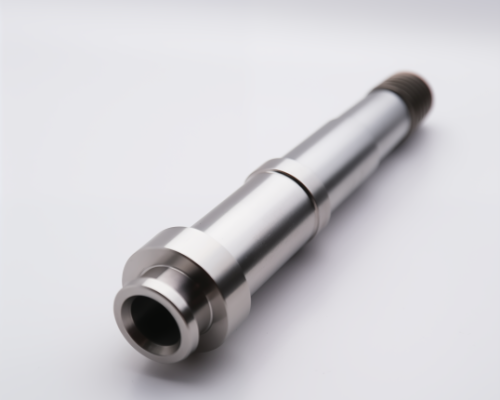
4.Small Batch Sizes
Small batch sizes in CNC machining represent a significant cost factor when pursuing ultra-smooth finishes, particularly for orders of just a few parts. This cost impact occurs because the extensive setup time, programming, and quality control procedures required for achieving high-quality finishes must be spread across fewer parts, resulting in higher per-unit costs.
Single Part Costs
Prototyping or producing individual parts with fine surface finishes (Ra 0.8 μm) can cost between $200-500 per part due to the concentration of setup costs. This high cost stems from several factors:
- Initial machine setup and programming time remains the same whether producing one part or many
- First article inspection and quality control procedures must be performed regardless of quantity
- Tool wear and machine time costs are not distributed across multiple parts
- Surface finish validation and measurement processes require the same effort for single parts
Impact on Per-Unit Costs
Increasing batch sizes can dramatically reduce per-unit costs through economies of scale. A part that costs $500 to produce as a single unit might cost only $100-200 per unit in larger quantities, representing a 60-80% reduction in per-unit cost. This reduction occurs because:
- Setup times and costs are distributed across more parts
- Operators become more efficient with repeated operations
- Quality control procedures can be streamlined for batch production
- Tool costs are amortized over multiple parts
- Surface finish optimization can be fine-tuned over multiple pieces
Batch Size Optimization
Batch Size Cost Per Unit Setup Time Impact Quality Control Impact
1-5 units Base cost (highest) Full setup per part Individual inspection
6-25 units -30-40% Shared setup costs Sampling approach
26-50 units -50-60% Optimized setup Statistical process control
50+ units -60-80% Maximum efficiency Automated inspection
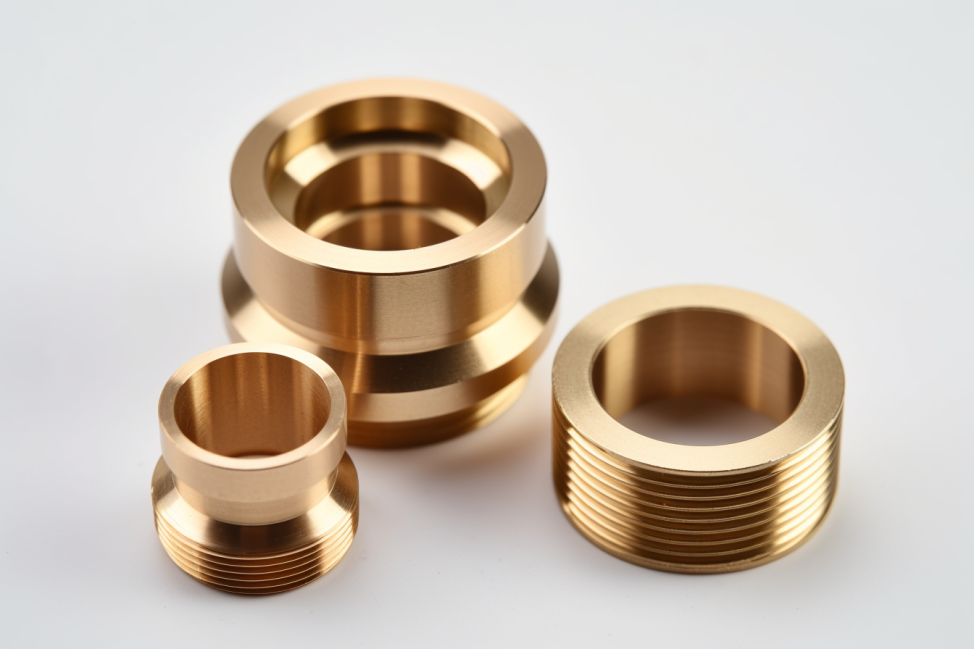
5. Suboptimal Toolpath Strategies
Suboptimal toolpath strategies represent inefficient machining approaches when achieving ultra-smooth finishes. This occurs when manufacturing processes use overly cautious or inefficient cutting parameters, leading to unnecessarily long machining times and increased costs without proportional quality benefits.
Conservative Feeds/Speeds
Overly cautious machining parameters, such as using a 0.1mm depth of cut when the tool and material could handle more aggressive cuts, significantly extend production time. These conservative approaches often stem from:
- Fear of tool breakage or surface finish deterioration
- Lack of optimization data for specific material-tool combinations
- Default use of generic cutting parameters For example, a finishing operation that could be completed in 30 minutes with optimized parameters might take 45-60 minutes with overly conservative settings, directly increasing machining costs without improving surface quality.
Tool Wear Considerations
Using standard carbide tools instead of diamond-coated or other advanced tooling options for high-volume precision machining leads to:
- More frequent tool changes
- Inconsistent surface finishes as tools wear
- Increased machine downtime For instance, standard carbide tools might need replacement after every 3-4 parts when machining abrasive materials, while diamond-coated tools could maintain surface finish quality for 12-15 parts before replacement.
Diamond-Coated vs. Standard Tools (3x difference)
Tool Type Life Span Surface Consistency Cost Impact
Standard Carbide Base life Variable with wear Base cost
Diamond-Coated 3x longer Consistent -25% long-term
CBN/PCD Tools 5x longer High consistency -40% long-term
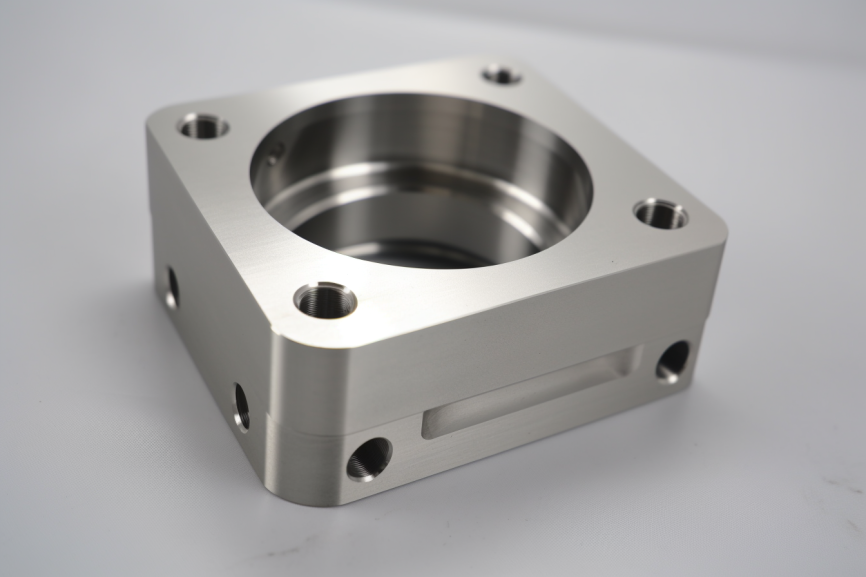
Cost-Reduction Strategies
Implementing strategic approaches to reduce costs while maintaining high-quality surface finishes can lead to significant savings in CNC machining operations. Here are four proven strategies that can help optimize your manufacturing costs without compromising quality.
Adopt DFM Principles
Design for Manufacturing (DFM) principles focuses on simplifying geometries to reduce machining complexity and time. Key implementations include:
- Eliminating unnecessary undercuts that require special tooling
- Designing parts with standard tool sizes in mind
- Minimizing the number of setups required
- Incorporating appropriate draft angles These modifications can significantly reduce machining time while maintaining functionality, leading to substantial cost savings in the production process.
Optimize Batch Production (50+ units)
Ordering in larger quantities helps amortize setup costs effectively. When producing 50 or more units:
- Setup costs are distributed across more parts
- Process optimization becomes more economical
- Tool life is better utilized
- Quality control procedures become more efficient For example, a part that costs $400 in single-unit production might drop to $100-150 per unit in a 50+ piece order, offering significant economies of scale.
Leverage COTS Components
Using Commercial Off-The-Shelf (COTS) components instead of custom-machined parts where possible can dramatically reduce costs. This strategy involves:
- Identifying standard parts that can replace custom components
- Using standardized fasteners and bushings
- Incorporating readily available hardware This approach not only reduces manufacturing costs but also improves repair and replacement efficiency.
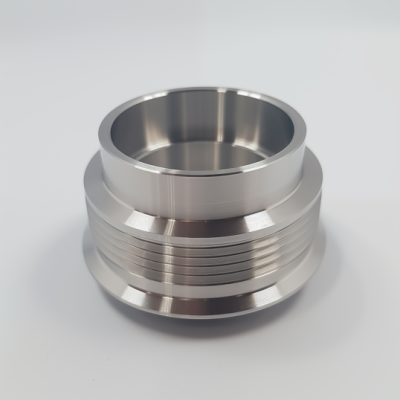
Relax Tolerances (±0.001" to ±0.005" - 30% savings)
Strategic tolerance adjustment where functionally appropriate can yield substantial savings:
- Identify non-critical dimensions where tolerances can be relaxed
- Maintain tight tolerances only where functionally necessary
- Use standard tolerances (±0.005″) instead of precision tolerances (±0.001″) where possible This approach can reduce machining time and costs by approximately 30% without compromising part functionality.
Strategy Typical Savings Implementation Time
DFM Principles 15-25% Design Phase
Batch Optimization 60-80% Production Planning
COTS Integration 20-30% Design Phase
Tolerance Optimization 25-30% Engineering Review
Conclusion
Understanding these five key areas of CNC machining cost inflation – from surface specifications to toolpath strategies – enables manufacturers to optimize production costs while maintaining quality. By implementing strategic cost-reduction approaches, companies can achieve 20-40% savings without compromising the ultra-smooth finishes their applications demand.
Frequently Asked Questions
An ultra-smooth CNC finish typically refers to surface roughness values of Ra ≤0.4 μm. This level of finish often requires additional post-machining processes like polishing and is commonly used for optical components or aesthetic surfaces.
Ultra-smooth finishes can increase manufacturing costs by 15-20% compared to standard machined surfaces, primarily due to additional post-processing steps and longer machining times. This cost increase can be higher when combined with complex geometries or hard-to-machine materials.
Ultra-smooth finishes are necessary for applications involving optical components, precision mating surfaces, or parts requiring specific aesthetic qualities. They’re essential for components like medical devices, optical instruments, or high-end consumer products where surface quality directly impacts functionality.
While ultra-smooth finishes are possible on most materials, the difficulty and cost vary significantly. Softer materials like aluminum are easier to finish, while harder materials like titanium or stainless steel require more time, specialized tools, and often additional processing steps.
Evaluation should focus on the functional requirements of each surface, including visibility, component interaction, and performance requirements. Comparing these needs with standard surface roughness tables helps identify where specifications might exceed functional requirements.
Production runs of 50+ units typically offer the best cost efficiency for ultra-smooth finished parts. This batch size allows for optimal setup cost distribution and process optimization, potentially reducing per-unit costs by 60-80% compared to single-unit production.