In manufacturing, processes range from CNC machining to additive manufacturing. Yet, the production volume—whether for custom products or mass production—stands out as a key determinant. It affects cost, time-to-market, and raw material choices.
Table of Contents
The Basics of Volume Production
What is Low Volume Production?
Low-volume production bridges prototype development and high-volume output. It’s ideal for short-lived products or those entering the market. Rapid prototyping and urethane casting allow cost-effective production without expensive tooling, facilitating quick feedback and market entry.
How is High Volume Production Different?
High-volume production, synonymous with mass production, focuses on large quantities. Leveraging automated processes and specialized tools, it achieves economies of scale. It’s common for products with consistent demand and is cost-effective per unit, despite higher initial tooling costs.
Why Choose Between Low and High Volume?
The choice between low and high volumes in manufacturing influences method, tooling investment, production speed, and post-processing. It’s crucial for product developers, whether testing a concept or aiming for large-scale output.

Low Volume Production: A Deep Dive
What Exactly is a Rake Angle?
Low-volume production isn’t just a middle ground between prototyping and mass production; it’s a strategic choice for many manufacturers. Here’s why:
- Faster Market Penetration: Launching products in smaller batches means quicker feedback and the ability to adapt, ensuring a more successful market entry.
- Reduced Investment Risk: Instead of pouring resources into large-scale production, manufacturers can test the waters, reducing financial risks.
- Flexibility in Design Refinement: Small-scale production allows for tweaks based on real-world feedback, ensuring the final product meets market needs.
Low Volume Manufacturing Methods
Different products require different manufacturing methods. Here are some of the most common techniques for low volume production:
– CNC Machining: Ideal for precise parts, CNC machining offers high accuracy and a wide range of materials.
– Rapid Prototyping: Speed is the name of the game. This method allows quick model creation to test form, fit, and function.
– Urethane Casting: Perfect for producing parts without metal tooling, it’s a cost-effective method for plastic parts.
– Sheet Metal Fabrication: This method offers durability and precision for products requiring metal components.
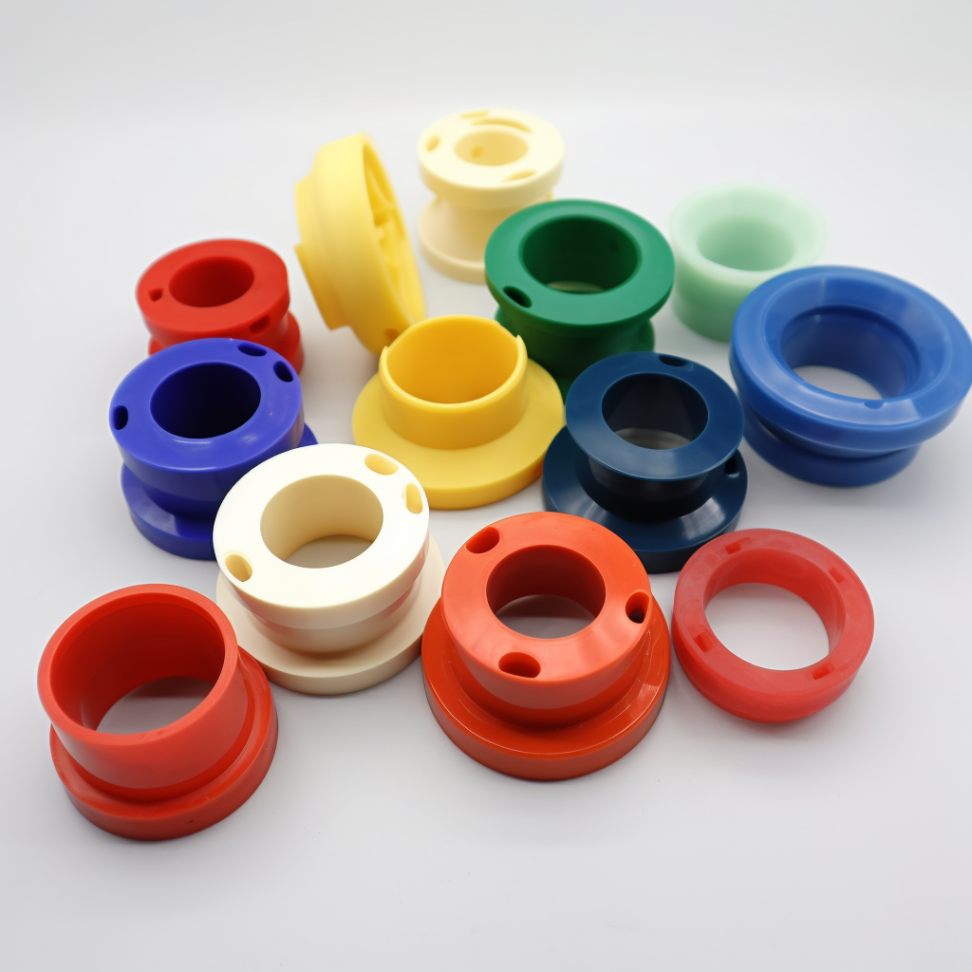
The Significance of the Prototyping Phase
Prototyping isn’t just about creating a model; it’s a crucial phase in low volume production. It allows manufacturers to test and refine their designs, ensuring the final product is functional and market-ready.
Cost-Effective Solutions and Tooling
Low volume production is synonymous with cost-effective solutions. Manufacturers can save money by avoiding expensive high-volume tooling while producing high-quality parts. The emphasis on cost-effective tooling ensures that even with smaller batches, profitability isn’t compromised.
Low Setup
One of the standout advantages of low volume production is the reduced setup time. With quicker changeovers and less downtime, manufacturers can efficiently produce small quantities, ensuring timely delivery and high product quality.
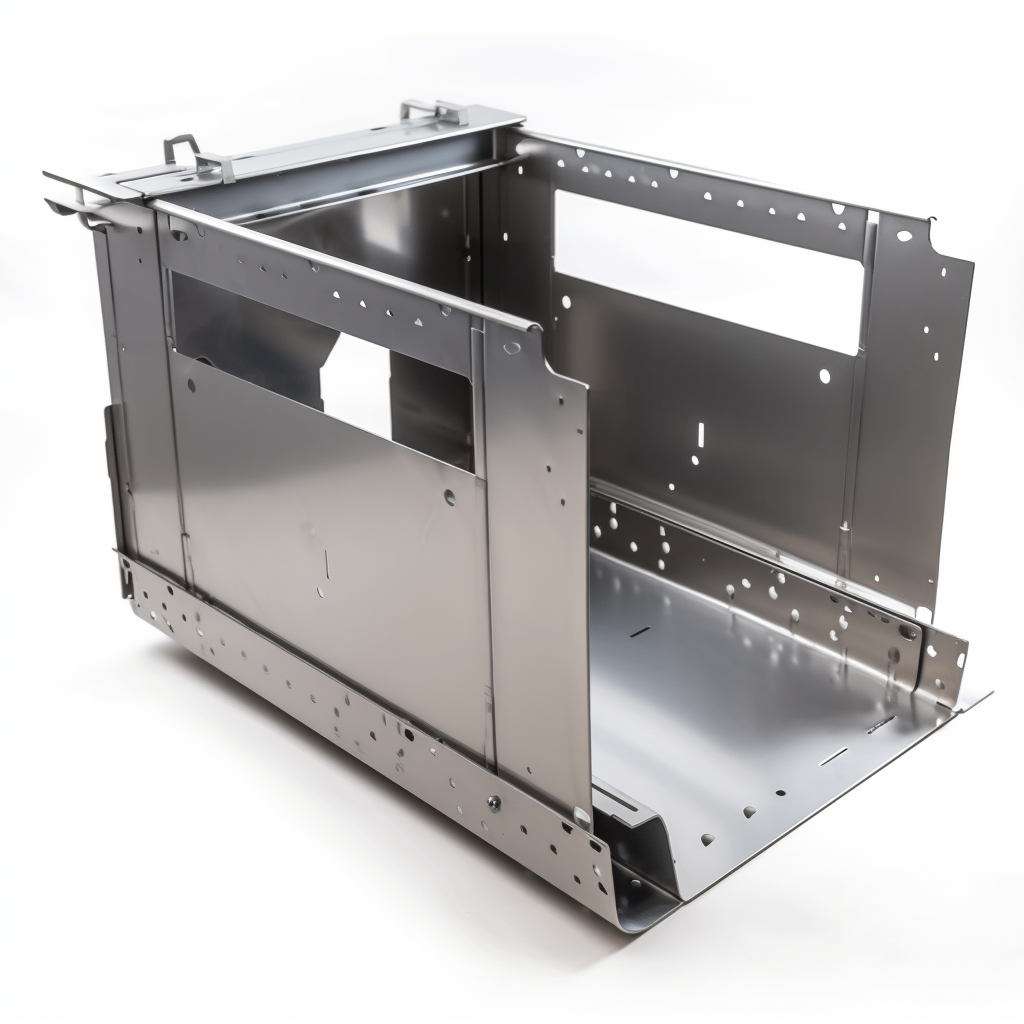
High Volume Production: Scaling Up
Transitioning from Low to High Volume Production
Starting with low volume production services allows manufacturers to test the waters, gather customer feedback, and refine their product. But when the demand surges and the market is ripe, transitioning to full-scale production becomes the next logical step. This shift from a low volume starting point to large scale manufacturing is a significant milestone in the product development cycle.
Advantages of High Volume Production
Scaling up production comes with its set of benefits:
- – Economies of Scale: As production runs increase, the cost per unit often decreases, leading to higher profit margins.
- – Commercial Success Potential: High volumes often mean a product has achieved market acceptance, paving the way for commercial success.
- – Automated Manufacturing Processes: High volume manufacturing often leverages automated processes, like injection molding and CNC machines, ensuring consistency and quality.
Challenges in Scaling Up
While high volume production offers many benefits, it’s not without its challenges:
– Expensive High Volume Tooling: The initial setup, especially tooling, can be costly. However, spread over high volumes, these costs can be justified.
– Material Shortages: Managing raw materials becomes crucial, especially when producing parts in large quantities. Material shortages can halt production, so having a reliable contract manufacturer and a backup plan is essential.
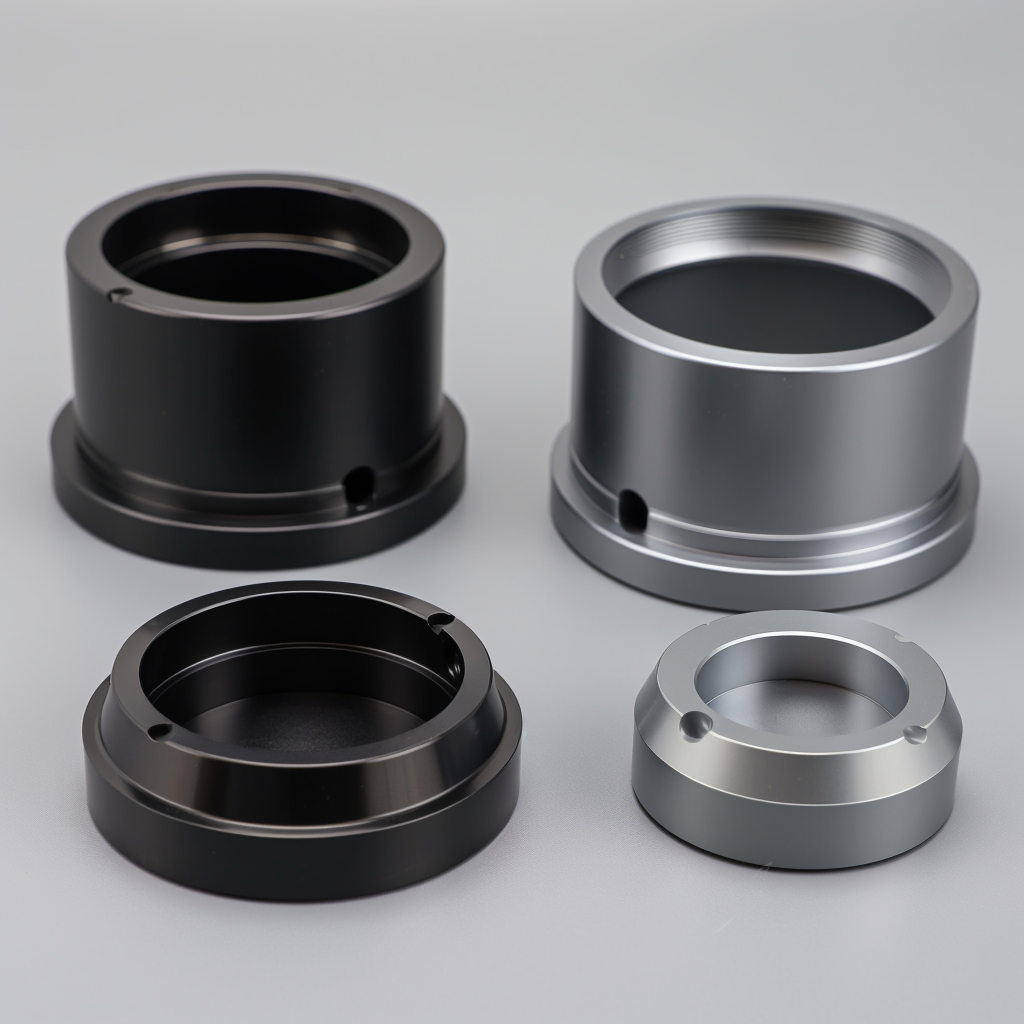
Precision in High Volume Manufacturing
In high volume manufacturing, precision is paramount. The master pattern, often created using printing technology, is the benchmark for all subsequent parts. Tight tolerances ensure that every part produced matches the master pattern to a high degree, ensuring consistency across all production runs.
Low VS High Volume Production
Low volume focuses on flexibility and customization, often with higher per-unit costs, while high volume aims for cost efficiency through mass production.
How Do Cost Implications Differ?
Low volume production, often associated with prototype development and shorter product life cycles, allows manufacturers to save money initially. Manufacturers can test their products without a hefty investment by avoiding costly tooling and focusing on producing functional prototypes.
On the other hand, high volume production aims to reduce the cost per unit with its high setup costs. The initial investment in tools and CNC machines might be higher, but it becomes more cost-effective when spread over many parts.
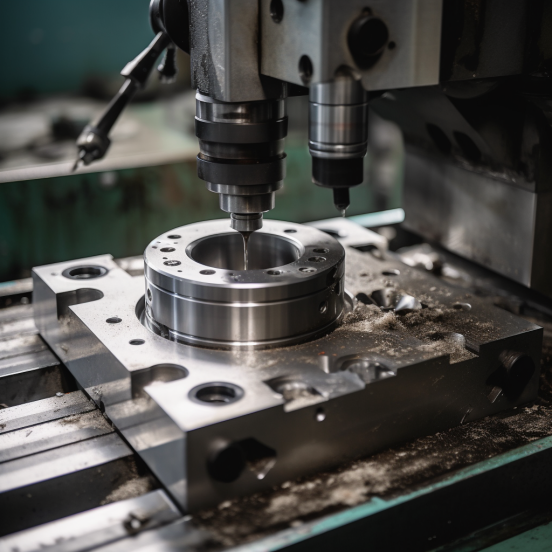
What About Time-to-Market?
Low volume manufacturing services prioritize getting to the market faster. With a focus on producing parts quickly, manufacturers can introduce their products to the market, gather feedback, and make necessary refinements. High volume production, with its intricate manufacturing processes, emphasizes marketing products quickly once production begins. The process might be longer, but the production rate is much higher once set up.
How Does Customization Vary?
Low volume production parts offer a high degree of customization. Manufacturers can cater to specific client needs, producing custom products with the same materials used in full volume production.
High volume, on the other hand, leans towards mass production. While there might be less room for customization, the consistency and uniformity of metal parts, especially in a high mix production environment, are unparalleled.
Which Offers More Flexibility?
In low volume manufacturing, feedback is immediate. When a product developer introduces a new project to the market, they can gather insights and refine based on real-world usage. This is crucial for products with shorter life cycles or niche markets.
High volume production, focusing on producing vast quantities, relies more on initial feedback before production begins. The emphasis is on getting it right the first time, ensuring that each product, from the first to the last, meets the set standards.

Challenges and Solutions in Volume Production
Challenges include managing high tooling costs, material shortages, and consistent quality. Solutions involve strategic planning, partnerships, and leveraging specialized manufacturing methods.
How to Address Tooling Costs?
Tooling costs can be a significant investment, especially in high volume production. However, strategies like using CNC machines can help reduce costs. In low volume production, manufacturers often opt for methods that don’t require expensive tooling, ensuring a cost-effective production process.
What Strategies Help Manage Material Shortages?
Material shortages can halt production, leading to delays and increased costs. Manufacturers often rely on forecasting and maintaining a buffer stock. Additionally, having a reliable contract manufacturer can ensure a steady supply of materials, ensuring that production runs remain uninterrupted.
How Do Contract Manufacturers Aid in Production?
Contract manufacturers play a crucial role in managing production runs. They bring expertise, resources, and scalability to the table. Whether it’s a need to market quickly or manage the next project’s production, contract manufacturers ensure the manufacturing process is efficient and meets the desired standards.
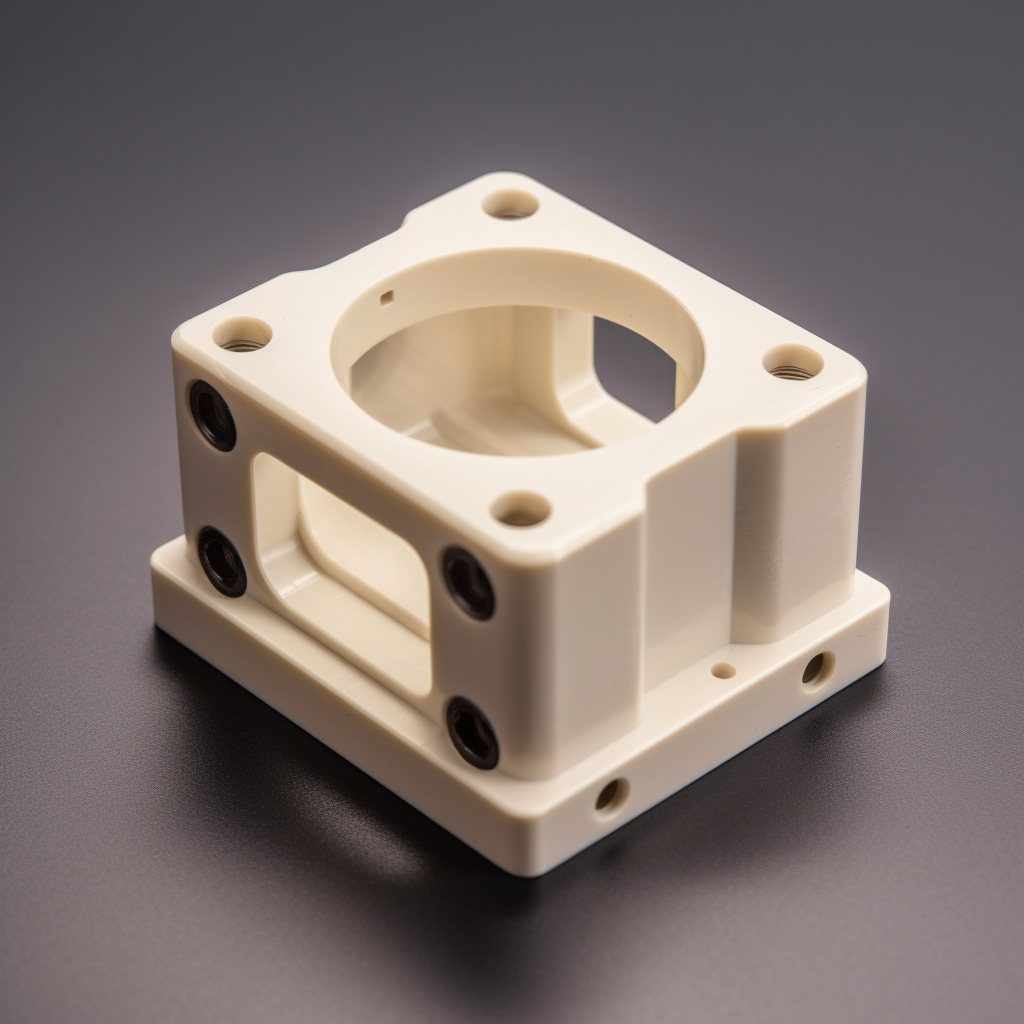
Conclusion
The future of manufacturing leans towards shorter product life cycles, emphasizing the need for flexibility. The low-volume manufacturing method offers adaptability, especially when tools like CNC machining are employed to reduce costs. As manufacturers plan their next project, choosing the appropriate low or high volume becomes pivotal for efficiency and market relevance.
Frequently Asked Questions
Low volume production techniques include CNC machining, rapid prototyping, urethane casting, and sheet metal fabrication. These methods are preferred for producing items in small quantities, often without significant engineering, design, or tooling investment.
The benefits of low volume production encompass the ability to turn production quickly, create custom products, and produce small run items. It also offers the flexibility to test new designs without incurring extensive up-front costs related to design or tooling development.
High volume production is geared towards mass-producing products quickly and efficiently, often for high-demand items. In contrast, low volume production focuses on producing products in smaller quantities, allowing for more flexibility, especially in the early stages of development or custom orders.
An example of a low volume business is a company that manufactures bicycle components using low-volume production methods. This approach provides more flexibility in the design process and can save manufacturing costs.
Low volume manufacturing offers several advantages, including the ability to turn production quickly, create custom products, and produce small run items. It also allows businesses to test new designs without significant up-front costs associated with design or tooling development.
Low volume manufacturing typically refers to an item produced in small quantities, often without significant engineering, design, or tooling investment. A low-volume production run might be any order with less than 100 units, though this can vary depending on the company.
Production volume can be calculated by multiplying the number of units produced by the time taken for production. It’s essential to consider factors like machine uptime, efficiency, and production runs to get an accurate measure.